Spis treści
- Przepisy i normy
- Projekt a powłoki antykorozyjne
- Powłoki antykorozyjne – przygotowanie powierzchni
- Malowanie
- Odbiór powłok malarskich
- Naprawy malarskich powłok antykorozyjnych
- Malowanie renowacyjne – powłoki antykorozyjne i ogniochronne
Przepisy i normy
Jak w każdej dziedzinie związanej z budownictwem podstawowym dokumentem jest „Prawo budowlane” oraz przepisy z nim powiązane, w tym normy. Zazwyczaj z jednej wytycznej może wynikać kilka, a nawet kilkadziesiąt następnych i z nich kolejne. Poniżej najważniejsze dokumenty związane z zabezpieczeniem, a także przed korozją i bierną ochroną przeciwpożarową konstrukcji stalowych hal:
- PN-EN 1090-2:2018-09 „Wykonanie konstrukcji stalowych i aluminiowych. Część 2: Wymagania techniczne dotyczące konstrukcji stalowych”;
- PN-EN ISO 129441 „Farby i lakiery. Ochrona przed korozją konstrukcji stalowych za pomocą ochronnych systemów powłokowych”: – Część 1:2018-01 „Ogólne wprowadzenie”, – Część 2:2018-02 „Klasyfikacja środowisk”, – Część 3:2018-02 „Zasady projektowania”, – Część 4:2018-02 „Rodzaje powierzchni i sposoby przygotowania powierzchni”, – Część 5:2020-03 „Ochronne systemy malarskie”;
- PN-ISO 85012 „Przygotowanie podłoży stalowych przed nakładaniem farb i podobnych produktów. Wzrokowa ocena czystości powierzchni”: – Część 1:2008 „Stopnie skorodowania i stopnie przygotowania niepokrytych podłoży stalowych oraz podłoży stalowych po całkowitym usunięciu wcześniej nałożonych powłok”, – Część 2:2011 „Stopnie przygotowania wcześniej pokrytych powłokami podłoży stalowych po miejscowym usunięciu tych powłok”, – Część 3:2008 „Stopnie przygotowania spoin, krawędzi i innych obszarów z wadami powierzchni”;
- PN-EN 13501-1+A1:2010 „Klasyfikacja ogniowa wyrobów budowlanych i elementów budynków. Część 1: Klasyfikacja na podstawie wyników badań reakcji na ogień”.
Przy zabezpieczeniach ogniochronnych należy brać pod uwagę europejskie wymagania zawarte w dokumentach EAD 350402- -00-1106 „Powłoki reaktywne do ochrony przeciwpożarowej elementów stalowych” oraz EAD 350140-00-1106 „Wyroby ochronne przeciwpożarowe i zestawy ochronne przeznaczone do zastosowań ognioodpornych”. Wynika to z faktu, że krajowe aprobaty techniczne są coraz częściej zastępowane przez dokumenty obowiązujące na terenie Unii Europejskiej.
- PN-EN ISO 1090 zawiera podstawowe wytyczne dotyczące wykonywania konstrukcji.
Część 2 liczy ok. 200 stron i określa wymagania dla konstrukcji stalowych lub elementów wytwarzanych z następujących wyrobów hutniczych:
- walcowanych na gorąco z gatunków stali nie wyższych niż S690,
- kształtowników i blach profilowanych na zimno z gatunków stali nierdzewnych nie wyższych niż S700 lub z węglowych
- nie wyższych niż S690,
- wyrobów formowanych na gorąco lub zimno ze stali nierdzewnej austenitycznej, austenityczno-ferrytycznej i ferrytycznej,
- kształtowników zamkniętych formowanych na gorąco lub na zimno, znormalizowanych i profilowanych indywidualnie, oraz kształtowników zamkniętych spawanych.
Norma może również być stosowana do konstrukcji ze stali konstrukcyjnej gatunków nie wyższych niż S960, pod warunkiem że wykonanie będzie dopasowane do kryteriów niezawodności i że zostaną określone wszystkie niezbędne wymagania dodatkowe. W punkcie 2.7 „Ochrona przed korozją” wymieniono większość ze wskazanych wcześniej norm, a dodatkowo EN 146161 (zastąpiona przez PN-EN ISO 12679:2015-12), PN-EN 15311 (zastąpiona przez PN-EN ISO 12670), PN-EN ISO 1461 i PN-ENISO 2063.
Dotyczą one powłok metalizacyjnych i ze względu na rozległość zagadnienia nie omówiono ich w niniejszym artykule. W punkcie 4.1.3 „Stopnie przygotowania powierzchni” powołano się na stopnie przygotowania P1, P2 i P3, wynikające z normy PN-EN ISO 8501-3.
Warto jeszcze zwrócić uwagę na rozdział 8.4 „Przygotowanie styków w połączeniach ciernych”. Połączenia skręcane elementów konstrukcyjnych są wyjątkowo niekorzystne dla powłok ochronnych. Większość farb w tych miejscach ulega zniszczeniu (zmiażdżeniu), pęka lub „wypływa” pod wpływem dużych sił ściskających.
Pozostawienie typowych powłok na stykach może zmniejszać współczynnik tarcia, co z kolei osłabia połączenie. Dlatego styki w połączeniach ciernych, w tych miejscach, gdzie będą podkładki pod śruby, powinny być potraktowane w sposób specjalny. Dla połączeń klasy B zalecane jest pokrywanie powierzchni powłokami metalizacyjnymi natryskiwanymi cieplnie lub malowanie ich farbami alkilokrzemianowo-cynkowymi na grubość 50–80 μm.
Zasadnicze aspekty ochrony przed korozją konstrukcji omówiono w ww. normie w rozdziale 10 „Zabezpieczenie powierzchni” i w załączniku F. W części dotyczącej zabezpieczeń przy użyciu farb odwołano się do norm dotyczących ochrony przed korozją. W dalszej części przedstawiono wszystkie ważniejsze operacje wynikające z tych przepisów, związane z zabezpieczeniem powłokowym, w tym przypadku malowaniem konstrukcji hal stalowych.
Polecany artykuł:
Projekt a powłoki antykorozyjne
Projekt hali o konstrukcji stalowej powinien zawierać dział dotyczący powłok antykorozyjnych, a jeżeli klasa odporności ogniowej obiektu jest wyższa niż E, również projekt zabezpieczeń ogniochronnych3.
Opracowanie zabezpieczenia antykorozyjnego konstrukcji powinno w pierwszej kolejności określać kategorię środowiska korozyjnego, na jakie będzie narażona konstrukcja zgodnie z PN-EN ISO 12944-2. Zdefiniowano ich sześć w zależności od szybkości postępowania korozji mierzonej ubytkiem stali lub cynku.
- Kategoria C1 to wnętrze budynków ogrzewanych, w których ubytek masy w ciągu roku nie przekracza 10 g/m² powierzchni stali.
- Kategoria CX – to najbardziej agresywne środowisko morskie i przemysłowe, gdzie wynosi on powyżej 1500 g/m².
Większość hal stalowych pracuje w środowiskach C2 i C3, tzn. o małym i średnim narażeniu na korozję, ale oczywiście są wyjątki wynikające z przeznaczenia i miejsca posadowienia obiektów. Określenie kategorii korozyjności jest ważne, bo od niej będzie zależał poprawny dobór systemu ochronnego – rodzaju i grubości powłok malarskich. Dalszym etapem projektu jest weryfikacja rozwiązań konstrukcyjnych pod względem poprawności oczyszczenia i zabezpieczenia elementów.
Niestety w odniesieniu do ochrony przed korozją błędy popełniane są tak często, że opracowano normę zalecającą określone rozwiązania projektowe, ułatwiające poprawne zabezpieczenie konstrukcji, i zakazującą tych „sprzyjających korozji” – PN-EN ISO 12944-3.
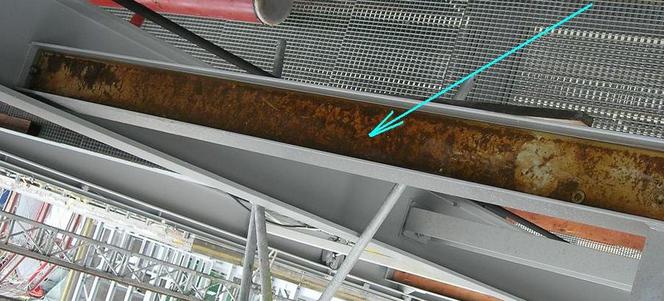
i
W przypadku ochrony przed korozją błędy konstrukcyjne mają znaczący wpływ na trwałość konstrukcji. Dla zabezpieczeń ogniochronnych te błędy mogą być bardziej groźne i uniemożliwiać zabezpieczenie konstrukcji przed skutkami pożaru.
Oglądając projekty hal przeznaczonych do zabezpieczenia ogniochronnego, bardzo często odnosi się wrażenie, że projektant uznał, iż wystarczy konstrukcję pomalować farbą, która ma odpowiednie dokumenty potwierdzające jej przydatność do ochrony, np. na R30, i na tym zakończył temat. Niestety to dość częsty błąd, ponieważ nie każdą konstrukcję można w taki sposób zabezpieczyć.
- Przepisy dotyczące ochrony przeciwpożarowej budynków
- Wynajem hali. Co trzeba wiedzieć? Koszty wynajmu hali magazynowej i produkcyjnej, umowy
Konstruktor, który ma świadomość, że projektuje konstrukcję przeznaczoną do biernego zabezpieczenia ogniochronnego, powinien wiedzieć, w jakim zakresie masywności elementów konstrukcyjnych może się poruszać. Przy obliczeniach musi też uwzględnić sprawę temperatur krytycznych. Wraz ze wzrostem temperatury stal traci parametry nośne, np. przy ok. 570ºC jest w stanie przenieść tylko połowę obciążenia przenoszonego w 20ºC.
Poszukując materiałów do zabezpieczenia ogniochronnego, trzeba przygotować wykaz elementów konstrukcyjnych z określeniem założonej temperatury krytycznej, z podaniem ich masywności i funkcji w konstrukcji (belki lub słupy).
Konstrukcje „nadmiernie odchudzone” są z reguły zbyt wiotkie i nie da się ich zabezpieczyć przed skutkami pożaru przy pomocy farb, okładzin lub natrysków ogniochronnych. Projekt powinien także zawierać ogólne zalecenia dotyczące przygotowania powierzchni i doboru odpowiedniego systemu malarskiego (według normy PN-EN ISO 12944-5). Są one ściśle powiązane ze wspomnianą wcześniej kategorią korozyjności i zakładanym okresem trwałości systemu, który może być:
- krótki – do 7 lat,
- średni – od 7 do 15 lat,
- długi – od 15 do 25 lat,
- bardzo długi – powyżej 25 lat.
Dla środowisk korozyjności C2 i C3 zaleca się systemy malarskie z farb na bazie żywic alkidowych, akrylowych, epoksydowych i poliuretanowych, nanoszone 1-3 warstwami na grubość NDFT4 od 80 μm w środowisku o korozyjności C1 i C2 przy krótkiej trwałości, aż do 260 μm – dla trwałości bardzo długiej w środowisku C3.Grubości powłok są również uzależnione od rodzajów żywic oraz pigmentu antykorozyjnego w podkładzie. Przy trwałości bardzo długiej, w środowisku C3, stosując podkład pigmentowany cynkiem oraz kolejne powłoki z żywicy epoksydowej i poliuretanowe (opcjonalnie akrylowe), wystarczy NDFT 200 μm, a system o porównywalnej trwałości z farb na bazie żywic alkidowych lub akrylowych musi mieć NDFT 260 μm.
Powłoki antykorozyjne – przygotowanie powierzchni
O skuteczności zabezpieczenia antykorozyjnego decyduje dobór materiałów oraz ich właściwe zastosowanie. W przypadku farb ważne jest odpowiednie przygotowanie powierzchni i warunki aplikacji. Konstrukcja stalowa wymaga dwóch etapów prac przed malowaniem:
- właściwego przygotowania spawów, krawędzi i usunięcia ewentualnych wad z powierzchni stali. Szczegółowo zostało to ujęte w normie PN-ISO 8501-3. W skrócie chodzi o usunięcie w odpowiedni sposób wad spawalniczych, takich jak wżery, podtopienia czy rozpryski, oraz sfazowanie (lub lepiej zaokrąglenie) wszystkich ostrych krawędzi;
- oczyszczenia stali i nadania powierzchni odpowiedniego profilu umożliwiającego dobre „zakotwienie się” farb w podłożu. W przypadku elementów o ściankach grubszych6 niż 3 mm najlepsze efekty daje obróbka strumieniowo-ścierna. Zdecydowana większość producentów farb zaleca stopień czystości Sa 2½ (PN-ISO 8501) przy profilu chropowatości pośrednim (PN-ISO 8503-2). Elementy o cieńszych ściankach niż 3 mm mogłyby ulec uszkodzeniu podczas obróbki strumieniowo-ściernej, dlatego trzeba je przygotowywać poprzez szlifowanie lub obróbkę chemiczną.
Przygotowanie powierzchni ujmuje szeroko norma PN-EN ISO 12944-4. Przerwa pomiędzy czyszczeniem a malowaniem powinna być możliwie krótka, aby nie dopuścić do powstania tzw. rdzy nalotowej. Zanim zaczniemy malować, należy odpylić powierzchnię (PN-ISO 8502-3) i sprawdzić, czy jest ona zgodna z wymaganiami stawianymi przez producenta zastosowanej farby.
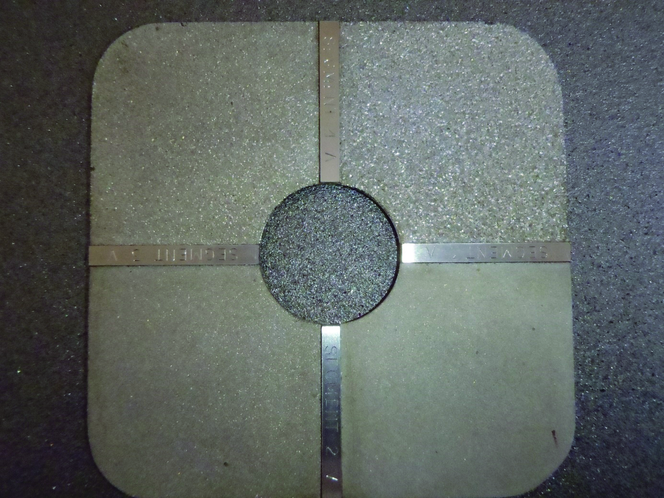
i
Malowanie
Samo malowanie, poza sprawdzeniem stanu powierzchni, trzeba poprzedzić kontrolą warunków klimatycznych, a więc temperatury stali i otoczenia, poziomu wilgotności oraz określeniem temperatury punktu rosy7. Producenci farb powinni podawać zalecane temperatury: malowanego podłoża, farby, otoczenia w trakcie schnięcia i utwardzania powłok. W karcie technicznej niemalże każdej farby jest zawarta formułka zabraniająca malowania, gdy różnica między temperaturą podłoża a temperaturą punktu rosy jest mniejsza niż 3ºC. Chodzi o to, aby nie zamalować wody, która w sposób niewidoczny może osadzić się na podłożu, ponieważ może to być przyczyną szeregu istotnych wad powłoki malarskiej, w tym znacznego osłabienia przyczepności farby do podłoża.
Powyżej wspomniano już o farbach takich, jak: alkidowe, akrylowe, epoksydowe, poliuretanowe oraz o specjalnych farbach podkładowych pigmentowanych cynkiem. Nie sposób krótko omówić istotnych różnic pomiędzy nimi. W skrócie można powiedzieć, że farby alkidowe to produkty jednoskładnikowe, które po wymieszaniu (w miarę potrzeby) z odpowiednim rozcieńczalnikiem od razu nadają się do użycia. Z reguły mają mniejszą trwałość i odporność na agresywne czynniki w porównaniu do epoksydowych, poliuretanowych oraz dwuskładnikowych farb akrylowych8. Farby dwuskładnikowe, takie jak epoksydowe czy poliuretanowe, wymagają znacznej staranności przy przygotowaniu. Trzeba zadbać o wymieszanie składników w zalecanych przez producenta proporcjach oraz przestrzegać czasu żywotności9 mieszanki. Kolejną sprawą jest wybór techniki aplikacji:
- pędzlem lub wałkiem,
- natryskiem powietrznym lub bezpowietrznym,
- metody mieszane i specjalne.
W przypadku dużych konstrukcji malowanie pędzlem lub wałkiem jest zbyt mało wydajne, dlatego stosuje się je wyłącznie do tzw. wyprawek malarskich, poprzedzających malowanie zasadnicze, oraz do napraw lokalnych uszkodzeń powłok.
Obecnie najbardziej rozpowszechnione stało się malowanie konstrukcji wielkogabarytowych natryskiem bezpowietrznym. Pompa malarska podaje farbę do pistoletu pod ciśnieniem od ok. 80 do nawet kilkuset barów. Rozpyla się, wydobywając się z dyszy odpowiedniego kształtu, rozprężając się i uderzając o powietrze. To w porównaniu z natryskiem powietrznym bardzo wydajny sposób malowania, generujący stosunkowo niskie straty, jednak estetyka powłok jest na ogół nieco słabsza. Na szczególną uwagę zasługuje aplikacja systemów ogniochronnych, składających się zazwyczaj z trzech warstw:
- podkładu antykorozyjnego,
- pęczniejącej farby (powłoki) ogniochronnej,
- farby nawierzchniowej, która zabezpiecza powłokę ogniochronną i pełni funkcję dekoracyjną.
Niektóre farby ogniochronne w określonych warunkach mogą tworzyć system samoistny lub występować tylko z podkładem. O skuteczności zabezpieczenia stanowi grubość położonej farby, która w zależności od czasu ochrony (R) i masywności elementu może wynosić od kilkuset mikrometrów do nawet kilku milimetrów. Nanoszenie tak grubych powłok wymaga odpowiednio mocnych pomp, mogących natryskiwać gęsty, z reguły zbrojony materiał. Na ogół takie grube powłoki nakłada się w kilku warstwach w odstępach jedno-, dwudniowych.
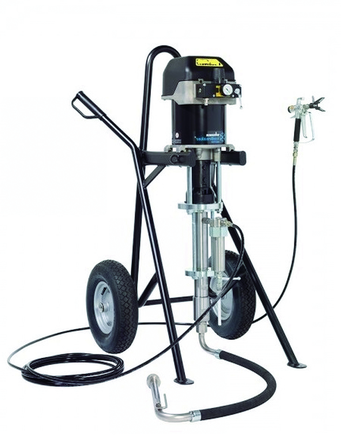
i
Odbiór powłok malarskich
W świetle obowiązujących norm9 podstawowym kryterium odbioru jest grubość powłoki, która powinna wynosić średnio nie mniej niż NDFT, jednak wynik pomiaru musi być pomniejszony o poprawkę korygującą na chropowatość. Zgodnie z tzw. zasadą 80/20 dopuszczalne są grubości mniejsze, wynoszące nie mniej niż 80% NDFT, ale ogólna liczba wyników pomiarów poniżej NDFT nie może stanowić więcej niż 20% wszystkich pomiarów. Dopuszczalne jest przekroczenie grubości NDFT do jej trzykrotnej wartości10. Należy też pamiętać, że w przypadku zabezpieczeń ogniochronnych grubości specyfikowane są minimalne i tu nie obowiązuje wspomniana wyżej zasada 80/20. Poza grubością może istnieć bardzo wiele kryteriów odbioru powłok malarskich, m.in.:
- aktualne dokumenty dopuszczające stosowanie farby lub zestawu farb w budownictwie11;
- wady dopuszczalne i niedopuszczalne,
- opis i maksymalne natężenie wad dopuszczalnych,
- przyczepność powłok (do podłoża i międzywarstwowa),
- kolor i połysk,
- ogólne wrażenie estetyczne.
Ważne jest, by te kryteria ustalić na początku prac, w przeciwnym razie może dochodzić do licznych nieporozumień pomiędzy wykonawcą a zleceniodawcą malowania.
Naprawy malarskich powłok antykorozyjnych
W trakcie transportu i montażu konstrukcji zawsze następuje uszkodzenie powłok malarskich. Najczęściej są to różnego rodzaju zadrapania i otarcia, czasem przepalenia na skutek spawania, cięcia lub szlifowania. Poprawnie wykonana naprawa jest bardzo ważna dla trwałości całego zabezpieczenia. Powinna ona polegać na usunięciu zniszczonych powłok, a jeżeli uszkodzenie doszło do podłoża, to również ewentualnych ognisk korozji, które mogły powstać w miejscach pozbawionych powłok. Bardzo ważne jest takie oczyszczenie powierzchni, aby pomiędzy powłoką nieuszkodzoną a podłożem zapewnić łagodne przejścia.
Należy też odpowiednio dobrać system naprawczy. Często jest to ten sam zestaw farb, co w systemie podstawowym, ale bywają grunty, np. farby etylokrzemianowe, których w warunkach polowych nie powinno się nakładać. W takiej sytuacji warto zwrócić się do producenta farb z prośbą o dobranie odpowiedniego zestawu naprawczego. Szczegóły dotyczące przygotowania podłoża do takich lokalnych napraw zawiera norma PN ISO 8501-2.
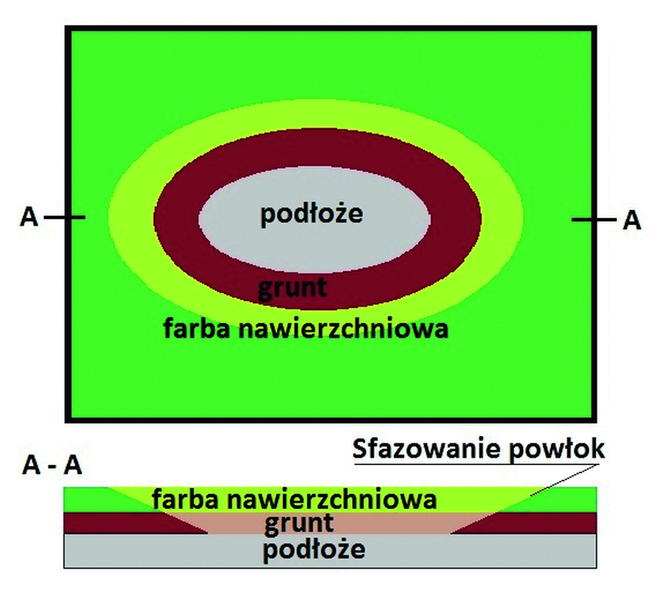
i
Malowanie renowacyjne – powłoki antykorozyjne i ogniochronne
Po przewidywanym okresie trwałości, o ile uszkodzenia powłok nie są większe niż założone kryteria, zalecane jest przeprowadzenie malowania renowacyjnego powłoki antykorozyjnej czy ogniochronnej. Powinno ono polegać na odpowiednim przygotowaniu powierzchni, najlepiej umyciu całości konstrukcji wodą pod wysokim ciśnieniem, oraz usunięciu lokalnych ognisk korozji, np. przez ich wyszlifowanie i naprawę odpowiednim gruntem epoksydowym (najlepiej takim, który toleruje ręczne nakładanie).
Samo malowanie renowacyjne w przypadku konstrukcji hal narażonych na środowiska C2 i C3 może ograniczyć się do nałożenia warstwy powłoki nawierzchniowej, np. farby poliuretanowej na grubość 40-60 μm. Może to wydłużyć pierwotny okres trwałości nawet o 2/3. Niestety rzadko się zdarza, by po kilkunastu lub kilkudziesięciu latach zachowała się dokumentacja z pierwszego malowania, dlatego bardzo ważne jest przeprowadzenie prób kompatybilności powłok, polegające na pomalowaniu niewielkiego fragmentu konstrukcji wybraną farbą i sprawdzeniu jej wpływu na pierwotną powłokę, a także wykonanie testów przyczepności pomiędzy starą a nową powłoką.
Przypisy
- 1 Norma aktualnie składa się z 9 części, celowo zostały pominięte części od 6 do 9, ponieważ dotyczą badań, nadzorów inspektorskich przy pracach związanych z malowaniem oraz ochrony konstrukcji dla platform wiertniczych.
- 2 Norma składa się z 4 części, ostatnia dotyczy czyszczenia wodą pod wysokim ciśnieniem i to zagadnienie pominięto.
- 3 W tym przypadku oznacza to klasy D, C i A. O klasie decyduje głównie przeznaczenie budynku oraz gęstość obciążenia ogniowego.
- 4 NDFT (ang. Nominal Dry Film Thickness) – nominalna grubość suchej powłoki.
- 5 Blachy i elementy o ściankach grubszych niż 3 mm są na ogół walcowane na gorąco, czego efektem jest trudna do usunięcia (innymi metodami niż obróbka strumieniowo-ścierna) zgorzelina walcownicza.
- 6 Temperatura punktu rosy to, w przypadku malowania, taka temperatura stali, przy której zaczyna dochodzić do wykraplania wilgoci na powierzchni.
- 7 Farby akrylowe mogą być jedno- i dwuskładnikowe.
- 8 Farby dwuskładnikowe nadają się do użytku przez ściśle określony czas. Po jego upływie ulegają zżelowaniu, co może m.in. doprowadzić do uszkodzenia sprzętu do malowania. Czas ten zależny jest od temperatury. W tzw. temperaturze pokojowej wynosi on z reguły kilka godzin.
- 9 Obecnie przy pomiarze grubości stosuje się dwie normy: PN ISO 19840 i PN-EN ISO 2808. Jeszcze do niedawna kryteria oceny grubości podawała PN-EN ISO 12944-5, nowe wydanie odwołuje się wyłącznie do ww. norm wspomnianych powyżej.
- 10 Istnieją pewne grupy farb, np. nieorganiczne grunty cynkowe, których grubość w stosunku do NDFT może być przekroczona tylko nieznacznie. W takim przypadku należy się opierać na zaleceniach producenta farby.
- 11 Od 1 stycznia 2021 farby lub grupy farb w systemie ochronnym muszą mieć aktualną Krajową Ocenę Techniczną (KOT).