Spis treści
Metody połączeń rur i kształtek z tworzyw sztucznych - np. PP, PP-R, PE, PE-HD, PE-RT, PE-X, PB lub PVC - w instalacjach można podzielić na dwie grupy:
- rozłączne – gdy istnieje możliwość wielokrotnego montażu oraz demontażu bez uszkodzenia elementów instalacji, np. połączenia rur gwintowe, kielichowe i kołnierzowe;
- stałe (nierozłączne) – jeśli po połączeniu elementów demontaż nie jest możliwy bez ich zniszczenia, dotyczy to m.in. klejenia, łączenia zaciskowego oraz zgrzewania.
Zgrzewanie stosuje się do łączenia prostych odcinków rur oraz odcinków rur z kształtkami umożliwiającymi połączenia kołnierzowe. Pod wpływem wysokiej temperatury i docisku łączone powierzchnie elementów tworzą jednolitą strukturę w miejscu połączenia.Wyróżnia się trzy podstawowe techniki zgrzewania:
- doczołowe,
- elektrooporowe,
- polifuzyjne (mufowe).
Wykorzystuje się je głównie w przypadku rur polietylenowych, polipropylenowych i polibutylenowych. Do wykonywania instalacji z użyciem rur z tych tworzyw sztucznych stosowane są różnego typu kształtki, m.in. mufki, kolana, trójniki, tuleje kołnierzowe, odgałęzienia siodłowe, zwężki, zaślepki. Wybór metody zależy przede wszystkim od średnicy i materiału łączonych elementów.
Rury z polietylenu
Rury z polietylenu są wykorzystywane w wewnętrznych instalacjach wody użytkowej oraz centralnego ogrzewania, a także w zewnętrznych sieciach np. wodociągowych, kanalizacyjnych ciśnieniowych i bezciśnieniowych, instalacjach podłączeń domowych wodociągowych, kanalizacyjnych, a także sieciach gazowych. Najczęściej są to systemy rur wykonanych z tzw. polietylenu sieciowanego (PE-Xa, PE-Xb lub PE-Xc), ale spotyka się również rury z polietylenu wysokiej gęstości (PE-HD) oraz liniowego o średniej gęstości (PE-RT).
W instalacjach wodociągowych można stosować rury z jednorodnego materiału (PE-X), jednak te do centralnego ogrzewania powinny mieć barierę antydyfuzyjną z żywicy EVOH bądź PVOH, która znacznie zmniejsza wnikanie tlenu do wnętrza instalacji. W przypadku instalacji ciepłej i zimnej wody użytkowej najpopularniejsze są kształtki zaciskowe, których montaż jest szybszy i łatwiejszy. Natomiast do zgrzewania rur z polietylenu wykorzystuje się kształtki przeznaczone do różnych technik łączenia: doczołowego, elektrooporowego i polifuzyjnego.
Rury o mniejszych średnicach można zgrzewać w każdy z trzech sposobów, ale najczęściej wykonuje się to metodą elektrooporową. Elementy o dużych średnicach (nawet 1000 i 1200 mm) bądź w trudno dostępnych miejscach zgrzewa się doczołowo lub przy użyciu muf elektrooporowych, a te stosowane w kanalizacji grawitacyjnej z polietylenu lub polipropylenu łączy się również poprzez tzw. spawanie ekstruzyjne (w przerwę pomiędzy rozgrzanymi końcami łączonych rur wtłacza się przy użyciu odpowiedniego sprzętu – ekstrudera – roztopiony materiał PE lub PP). Trzeba pamiętać, by nie zgrzewać doczołowo rur PE zwijanych w kręgi.
Rury z polipropylenu
Rury z polipropylenu najczęściej wykorzystuje się w wewnętrznych instalacjach wody użytkowej oraz centralnego ogrzewania. W tych drugich należy stosować warstwowe rury polipropylenowe, tzw. stabilizowane, które są odporne na podwyższoną temperaturę. W takiej wersji mają one warstwę/wkładkę: aluminiową (tzw. stabi – PPR-AL-PPR), z włókna szklanego (stabi glass – PPR-GF-PPR) lub włókna bazaltowego (z kopolimeru polipropylenu nowej generacji (typ 4) – PP-RCT).
Rury do wewnętrznych instalacji wody zimnej oznaczone są jako PN 10, PN 16 i PN 20, a do ciepłej użytkowej i grzewczych – PN 16 albo PN 20. Rury i kształtki systemowe polipropylenowe zwykle łączy się przez zgrzewanie polifuzyjne (mufowe). W przypadku elementów z włóknem szklanym lub bazaltowym nie jest wymagane zdzieranie (tzw. gradowanie) zgrzewanego fragmentu ścianek przed montażem, w przeciwieństwie do rur stabilizowanych warstwą aluminium, którą trzeba usunąć.
Rury z polibutylenu
Rury z polibutylenu stosuje się np. w wewnętrznych instalacjach wody użytkowej oraz centralnego ogrzewania, a także w zewnętrznych sieciach ciepłowniczych. Jeśli łączy się je poprzez zgrzewanie, to zwykle wykorzystuje się technikę polifuzyjną (mufową).
Zgrzewanie rur i kształtek rurociągów z tworzyw sztucznych należy przeprowadzać zgodnie z procedurami podanymi przez producentów – zarówno tych elementów instalacji, jak i zgrzewarek używanych do ich łączenia.
Przeczytaj również:
- Jakie instalacje z rur polietylenowych? Grzewcze, wodociągowe najkorzystniejsze
- Rozdzielacze w instalacjach grzejnikowych i ogrzewania podłogowego. Rodzaje, budowa, funkcje
- Narzędzia do zgrzewania rur i kształtek z tworzyw sztucznych
Zgrzewanie doczołowe rur i kształtek z tworzyw sztucznych
Poprzez zgrzewanie doczołowe można szybko połączyć elementy o tej samej średnicy nominalnej i grubości ścianki. Najczęściej w ten sposób spaja się rury polietylenowe o średnicy 63 mm i większe. Proces zgrzewania polega na współosiowym ustawieniu elementów, które mają zostać ze sobą zgrzane, a następnie ogrzaniu i uplastycznieniu ich końców oraz połączeniu ze sobą.
Do nagrzania końcówek elementów łączonych używa się najczęściej elektrycznych płyt grzejnych (nagrzanych do temp. 200–230°C), których płaszczyzny robocze muszą być płaskie i równoległe względem siebie, a rozkład temperatury na ich powierzchni nie może wykazywać różnic większych niż 10°C.
Trzeba pamiętać, by przed zgrzewaniem wyrównać i odtłuścić powierzchnie czołowe łączonych rur.Po usunięciu płyty grzewczej łączone elementy są do siebie dociskane i pozostawiane do naturalnego schłodzenia.
Proces zgrzewania powinien być wykonywany ściśle według instrukcji obsługi urządzeń do zgrzewania, dołączonej przez producenta. W czasie zgrzewania należy przestrzegać stabelaryzowanych wartości czasów poszczególnych operacji, temperatury płyty grzewczej (200–230°C) oraz ciśnienia docisku i posuwu.
Dokładne parametry zgrzewania powinny być podane przez producenta rur w instrukcji montażu. Są to m.in.:
- temperatura nagrzewania,
- ciśnienie docisku,
- czas nagrzewania,
- czas przestawienia,
- minimalna siła docisku zgrzewanych elementów,
- czas zgrzewania,
- wysokość wypływki,
- czas chłodzenia,
- wytrzymałość montażowa,
- pełna obciążalność zgrzeiny.
W przypadku złączy z naciskiem ręcznym (mechanicznym) wartości siły docisku można określić na podstawie tabel podawanych przez producentów. W przypadku urządzeń hydraulicznych zastosowane ciśnienie będzie zależeć od średnicy.
Zgrzewanie elektrooporowe rur i kształtek z tworzyw sztucznych
Zgrzewanie elektrooporowe to w pełni zautomatyzowany proces, często stosowany przy łączeniu prefabrykowanych fragmentów instalacji, przeróbek, napraw itp. Technika ta wymaga użycia specjalnych kształtek, które w korpusie mają umieszczony element grzewczy w postaci zwiniętego drutu oporowego. Istnieje wiele systemów kształtek elektrooporowych, m.in. mufy, trójniki, redukcje, trójniki, kolanka i zaślepki.
Trzeba pamiętać, by przed montażem przycięte prostopadle do osi rury końcówki rur oczyścić i odtłuścić na odpowiedniej długości podlegającej zgrzewaniu (decyduje średnica rury). Z rury trzeba też usunąć warstwę zewnętrzną (np. przy użyciu skrobaka) i zaokrąglić krawędź.
Wśród dostępnych na rynku rozwiązań wyróżnia się elektromufa (z pamięcią kształtu), stosowana do rur o średnicach 40–160 mm, która najpierw zostaje podgrzana, a następnie stygnie i zaciska się równomiernie na całej długości spoiny. Strefa nagrzania i topnienia materiału jest tu podzielona na dwa pola, gdyż w środkowej części kształtki nie ma drutu oporowego. Innym rodzajem kształtki jest termomufa – do większych średnic (200–315 mm) – wewnątrz której znajdują się bezpieczniki topikowe automatycznie odcinające napięcie, gdy zostanie osiągnięta wymagana temperatura zgrzania.
Przed rozpoczęciem zgrzewania należy zeskanować kod kreskowy znajdujący się na kształtce. Zawiera on informacje o parametrach zgrzewania (napięcie, czas zgrzewania oraz czas stygnięcia), które przekazywane są do zgrzewarki. Końce łączonych rur z obrobionymi płaszczyznami czołowymi wprowadza się do kielichów kształtek i łączy wtyki spirali oporowej z urządzeniem do zgrzewania. Zgrzewarka powoduje przepływ prądu przez kształtkę, a drut oporowy, rozgrzewając się do odpowiedniej temperatury, topi materiał. Powierzchnie elementów spajają się ze sobą w miejscu łączenia, tworząc szczelne i wytrzymałe złącze.
Po zakończeniu zgrzewania musi minąć tzw. czas chłodzenia zgrzewu, wskazany w tabeli parametrów podawanych przez producentów rur. Zazwyczaj po 24 godzinach od wykonania ostatniego zgrzewu można rozpocząć test hydrauliczny instalac
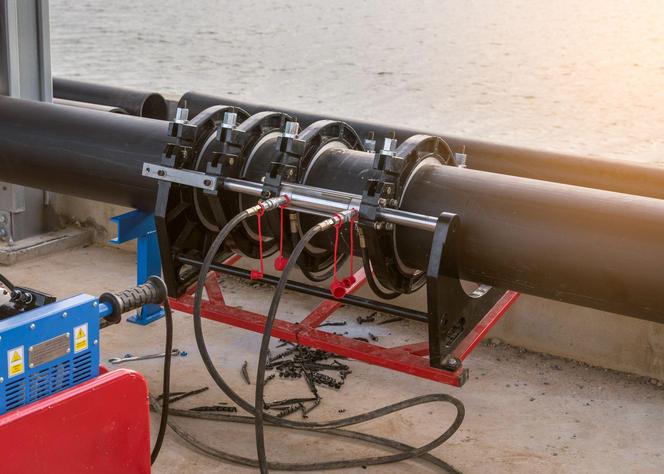
i
Zgrzewanie mufowe (polifuzyjne) rur i kształtek z tworzyw sztucznych
Zgrzewanie mufowe (polifuzyjne) z powodzeniem można zastosować podczas wykonywania instalacji wewnątrz budynków, np. mieszkalnych. W ten sposób najczęściej łączy się rury i kształtki polipropylenowe, a także polietylenowe, ale o niedużych średnicach. Potrzebna jest do tego elektryczna zgrzewarka polifuzyjna trzpieniowa lub płaska, wyposażona w wymienne kamienie grzejne (zwane też nakładkami, tulejami bądź matrycami) dla każdej średnicy, które nagrzewają jednocześnie zewnętrzną powierzchnię rury oraz wewnętrzną kształtki. Nagrzane elementy wsuwa się jeden w drugi na wymaganą głębokość.
Aby poprawnie wykonać skuteczne połączenie elementów polipropylenowych, przed rozpoczęciem zgrzewania trzeba przyciąć rurę prostopadle do jej osi przy użyciu nożyc lub obcinaka do rur tworzywowych. Konieczne jest także oczyszczenie i odtłuszczenie powierzchni, które będą łączone: zewnętrznej rury i wewnętrznej kształtki.
Ponadto w przypadku rur stabilizowanych aluminium należy usunąć zewnętrzną warstwę tworzywa oraz wkładkę aluminiową na odpowiedniej długości planowanego zgrzewu (zależnie od średnicy rury), np. za pomocą specjalnych zdzieraków. Długość zgrzewu warto wcześniej dokładnie odmierzyć i zaznaczyć na rurze, np. ołówkiem, a także sprawdzić odmierzoną głębokość poprzez umieszczenie rury w gnieździe kształtki.
Zaleca się również zaznaczyć na rurze i kształtce pozycję łączenia, aby w trakcie zgrzewania wyeliminować obracanie przewodu w kształtce. Na wewnętrznej powierzchni kształtki zazwyczaj znajduje się tzw. próg oporowy, umieszczony głębokości, która określa długość strefy objętej zgrzewaniem. Nie należy przekraczać głębokości zgrzewu, ponieważ spowoduje to utworzenie znacznej spoiny zgrzewczej zewnętrznej i wewnętrznej, co może prowadzić do zwężenia przekroju przepływu.
Rurę z przygotowaną końcówką oraz kształtkę wsuwa się osiowo w kamienie zgrzewarki nagrzanej do odpowiedniej temperatury. W celu zgrzania rur i kształtek PN 10 najpierw wsuwa się kształtkę, a dopiero po odliczeniu połowy czasu nagrzewania – rurę. Dla rur i kształtek PN 16 oraz PN 20 wsuwa się oba elementy jednocześnie.
Rura i kształtka muszą pozostać w kamieniach zgrzewarki przez czas nagrzewania odpowiedni dla danej średnicy. Po jego upływie zdejmuje się jednocześnie kształtkę i końcówkę rury z elementu grzewczego i natychmiast łączy ze sobą z zachowaniem współosiowości. Nie należy skręcać części podczas wykonywania złącza. Kiedy rura zostanie umieszczona w kształtce trzeba zachować czas łączenia – od momentu całkowitego wsunięcia rury w kształtkę aż do chwili utworzenia spoiny.
Połączone elementy trzeba przytrzymać nieruchomo przez 20–30 s, aż zgrzew osiągnie wstępną wytrzymałość. W dobrze wykonanym połączeniu na całym obwodzie obu części powinna występować wypływka. Takie połączenie utrzymuje się pod naciskiem osiowym przez okres równy czasowi nagrzewania, a następnie pozostawia do ostygnięcia. Czas chłodzenia to czas między końcem zgrzewania złącza (bez czasu manipulowania elementami) a rozpoczęciem następnego zgrzewania tej samej kształtki lub rury, na której się pracuje.
Podstawowe parametry zgrzewania polifuzyjnego, czyli m.in. czas nagrzewania, łączenia i chłodzenia oraz głębokość zgrzewania, producenci podają w instrukcjach. Przestrzeganie tych zaleceń zapewni uzyskanie jednorodnego połączenia, gwarantującego odpowiednią szczelność i wytrzymałość mechaniczną instalacji.
Zgrzewanie polifuzyjne (mufowe) rur polietylenowych dopuszcza się jedynie w warunkach warsztatowych, np. w celu przygotowania prefabrykatów (połączeń, węzłów) na budowę. Polega ono na równoczesnym nagrzaniu zewnętrznej powierzchni rury i wewnętrznej powierzchni kształtki do temperatury zgrzewania oraz ich zespoleniu.
Do montażu rur o średnicy do 63 mm używa się specjalnego elementu grzewczego z wymiennymi tulejami i króćcami, do większych rur – zgrzewarek stacjonarnych. Temperatura zgrzewania elementów polietylenowych metodą polifuzyjną powinna wynosić 250–270°C, a czas nagrzewania zależy od średnicy łączonych elementów i grubości ścianek.