W artykule:
- Pco wpływa na ich trwałość?
- Uszkodzenia posadzek przemysłowych
- Punktowe uszkodzenia posadzek przemysłowych
- Posadzki przemysłowe - uszkodzenia liniowe
- Posadzki przemysłowe - uszkodzenia powierzchniowe
- Posadzki przemysłowe a niska wytrzymałość podłoża gruntowego
- Posadzki przemysłowe a niska wytrzymałość betonu
- Zarysowania powierzchniowe posadzki przemysłowej
- Posadzki przemysłowe - podsumowanie
Co wpływa na trwałość posadzki przemysłowej?
Podłoga, wraz z posadzką stanowiącą jej wykończenie, jest jednym z głównych elementów obiektu budowlanego, a jej stan techniczny i właściwości użytkowe bardzo często decydują o przydatności budynku do konkretnych celów lub eksploatacji w ogóle. W zależności od przeznaczenia obiektu i lokalizacji podłogi (na gruncie lub na stropie) niezbędny jest prawidłowy dobór jej konstrukcji oraz górnej warstwy, która znajdować się będzie w bezpośrednim kontakcie z czynnikami decydującymi o szybkości jej zużycia. Uwzględniając różnorodność obciążeń i sił zewnętrznych działających na posadzkę, można przyjąć, że jest ona częścią obiektu najbardziej narażoną na uszkodzenia i zużycie. Na jej walory użytkowe i trwałość mają wpływ następujące uwarunkowania:
- precyzyjnie określone obciążenia i czynniki zewnętrzne zidentyfikowane na etapie opracowywania dokumentacji,
- prawidłowy projekt, uwzględniający działanie obciążeń statycznych, dynamicznych i udarowych, lokalne warunki gruntowo-wodne, a także jakość podłoża gruntowego, stopień zagęszczenia gruntu itp.,
- jakość użytych materiałów oraz ich właściwy dobór pod względem odporności na ścieranie, wrażliwości na działanie czynników agresywnych i wilgoci, łatwości konserwacji oraz mycia, a także klasy, konsystencji i pozostałych parametrów mieszanki betonowej,
- fachowe, zgodne z technologią wykonanie, obejmujące nie tylko właściwe ułożenie samej posadzki, ale również podkładu betonowego, jego pielęgnację oraz nacięcia, wypełnienia dylatacji itp.,
- właściwa, zgodna z założeniami projektowymi, eksploatacja, a przede wszystkim nieprzekraczanie założonych na etapie projektowania obciążeń mechanicznych, chemicznych i fizycznych oraz działania niekorzystnych czynników zewnętrznych,
- okresowe przeglądy i bieżące naprawy.
Uszkodzenia posadzek przemysłowych
Klasyfikuje się je różnorako, lecz przy doborze sposobu naprawy istotne jest ustalenie przyczyn powstania zniszczeń, ponieważ pozwala to na opracowanie prawidłowej metody ich trwałego usunięcia. Właściwe zdiagnozowanie źródła uszkodzenia posadzek to jednak dopiero wstęp do przyjęcia odpowiedniej metody naprawy, gdyż skuteczny i trwały sposób likwidacji powstałych wad powinien uwzględniać szereg innych czynników.
Jednym z ważniejszych jest ustalenie, czy przyczyna powstania uszkodzeń ustąpiła, czy też działa nadal, np. czy proces osiadania podłoża lub budynku uległ zakończeniu, czy też postępuje w dalszym ciągu albo czy powstałe pęknięcie osiągnęło już szerokość graniczną, czy też ma charakter dynamiczny. Dla potrzeb niniejszego opracowania przyjęto podział uszkodzeń oparty o ich kształty i wymiary, ponieważ czynniki te najczęściej determinują technologię naprawy i dobór materiałów. Zastosowano następującą klasyfikację uszkodzeń: punktowe, liniowe, powierzchniowe, spowodowane źle wykonanym podłożem gruntowym, związane z niską wytrzymałością betonu (strukturalne) oraz zarysowania powierzchniowe.
Patrz też:
Wszystkie wymienione rodzaje zniszczeń posadzek przemysłowych mogą występować pojedynczo lub, co zachodzi dosyć często, pojawiać się równocześnie. W takich sytuacjach niezbędna jest dokładna inwentaryzacja uszkodzeń wraz z określeniem ich źródła i w oparciu o taką identyfikację – dobór kompleksowego sposobu naprawy. Poniżej scharakteryzowano wyszczególnione wyżej typy uszkodzeń i zaproponowano metody ich usunięcia.
Punktowe uszkodzenia posadzek przemysłowych
Terminem tym nazwane będą takie ubytki posadzki, których powierzchnia jest niewielka, a stosunek długości do szerokości jest zbliżony do 1. Pojęcie to obejmuje zarówno płytkie, powierzchniowe odpryski, jak i głębsze, strukturalne zniszczenia.Z praktyki budowlanej wynika, że uszkodzenia punktowe są najczęściej wynikiem działania czynników zewnętrznych (np. udarów wywołanych upadkiem ciężkich narzędzi), błędów spowodowanych wadliwym składem mieszanki betonowej (zanieczyszczeniem kruszywa, reakcją alkaliczną) lub odspojeniem posypki od podłoża betonowego na skutek źle dobranego momentu jej wbudowania bądź zacierania.
W pierwszym przypadku są to przeważnie płytkie ubytki o głębokości od jednego do kilku milimetrów (odpryski betonu powstające np. od uderzenia narzędzi), natomiast druga z opisanych sytuacji generuje często uszkodzenia znacznie głębsze – o charakterze strukturalnym. Ubytki pochodzące ze źródeł zewnętrznych najczęściej tworzą się podczas użytkowania posadzki. Występują przede wszystkim w halach warsztatowych, gdzie obciążenia dynamiczne od twardych kółek wózków transportowych oraz metalowych narzędzi i urządzeń są naturalnym zjawiskiem. Należy tu podkreślić, że głębokość uszkodzeń związana jest zarówno z wartością działającej siły, jak i wytrzymałością betonu, z którego wykonana została posadzka betonowa.
Czytaj też:
Przyczyną głębokich, lokalnych ubytków, sięgających nawet kilku centymetrów, mogą być zanieczyszczenia organiczne znajdujące się w kruszywie, takie jak: margiel, węgiel drzewny, glina itp. Mechanizm powstawania uszkodzeń powierzchni w takim przypadku związany jest głównie z pęcznieniem tych materiałów – podczas układania betonu przemieszczają się w górną strefę posadzki i pod wpływem wilgoci często powiększają swoją objętość.
Nie mając zdolności wiązania z pozostałymi składnikami mieszanki betonowej, odspajają się od nawierzchni, powodując powstawanie w niej ubytków. Ostatnią z wymienionych przyczyn tworzenia się uszkodzeń punktowych jest reakcja alkaliczna, polegająca na reakcji kruszywa z alkaliami zawartymi w cemencie, znana pod nazwą AAR (ang. Alkali Aggregate Reaction). Jej bezpośrednim efektem są pęczniejące produkty tego procesu, przybierające postać uwodnionych krzemianów alkaliów, prowadzące do różnorakich uszkodzeń, a nawet zniszczenia betonu. W przypadku kruszyw niewęglanowych (stosowanych najczęściej do wykonywania nawierzchni przemysłowych) zachodzi reakcja alkaliów z krzemionką, która określana jest skrótem ASR (ang. Alkali Silica Reaction). Z kolei reakcję alkaliów z kruszywami węglanowymi oznacza się symbolem ACR (ang. Alkali Carbonate Reaction).
Patrz też:
Choć obydwie reakcje zostały opisane już w połowie XX wieku, to ich mechanizm nie został w pełni poznany. Najbardziej rozpowszechniony jest pogląd, że zachodzi na skutek kontaktu zawartych w cemencie rozpuszczalnych alkaliów z domieszkami do betonu oraz reaktywnymi formami krzemionki. Zjawisko to jest na tyle powszechne, że część producentów posypek informuje o konieczności doboru odpowiednich składników mieszanki betonowej na posadzkę, celem uniknięcia powierzchniowej degradacji betonu.
Zasadnicza większość stwierdzonych i rozpoznanych uszkodzeń betonu spowodowanych reakcjami alkalicznymi miała miejsce w halach, gdzie panowała temperatura zbliżona do pokojowej, a wilgotność otoczenia była stosunkowo wysoka i wynikała np. z częstego zmywania posadzki betonowej.
Z eksploatacyjnego punktu widzenia niezwykle istotny jest fakt, że reakcje AAR postępują w czasie. Oznacza to, że raz zapoczątkowany proces powierzchniowej degradacji posadzki będzie się pogłębiał. Nawet gdyby hipotetycznie założyć ograniczenie sprzyjających mu czynników zewnętrznych (temperatura pokojowa i wilgotność powyżej 80%), to powstałe ubytki będą się powiększały na skutek normalnej eksploatacji.Jeśli chodzi o metody naprawy uszkodzeń punktowych, to najogólniej można przyjąć, że płytkie, kilkumilimetrowe ubytki należy uzupełniać materiałami o bardzo wysokich parametrach przyczepności do podłoża. Warunek ten spełniają żywice chemoreaktywne (np. epoksydowe), a przy użyciu odpowiedniego gruntu mogą być także stosowane na podłoża o podwyższonej wilgotności.
Istotnym kryterium ich aplikacji jest odpowiednio wysoka wytrzymałość betonu, ponieważ do posadzki o niskich parametrach przyczepność żywicy będzie ograniczona, a wykonana naprawa nietrwała. Do tego typu prac stosowane są zazwyczaj żywice trzyskładnikowe (żywica, utwardzacz i wypełniacz mineralny, najczęściej kwarcowy). Obecność wypełniacza w postaci bardzo drobnego kruszywa pozwala nie tylko obniżyć koszt naprawy, ale również dostosować wytrzymałość materiału naprawczego do parametrów mechanicznych betonu, przez co obydwa materiały znacznie lepiej współpracują.
Nie zaleca się natomiast stosowania drobnoziarnistych szpachlówek mineralnych – nawet dodatek polimeru nie gwarantuje odpowiedniej adhezji i trwałości naprawy, szczególnie w przypadku bardzo płytkich ubytków – o głębokości kilku milimetrów. Przy głębszych uszkodzeniach (powyżej 1 cm) dobrym rozwiązaniem jest użycie materiałów mineralnych typu PCC. Poprzez swój charakter (mineralna baza i konieczność aplikacji poszczególnych składników na wilgotne podłoża) są one najbardziej kompatybilne z podkładem betonowym i zapewniają bardzo dobrą współpracę zaprawy naprawczej z uszkodzoną posadzką. Najlepsze efekty daje stosowanie rozwiązań kompleksowych, czyli użycie warstwy sczepnej i wypełniaczy należących do tego samego systemu.
Uszkodzenia liniowe posadzek przemysłowych
Za uszkodzenia liniowe posadzek przemysłowych można uznać takie ich usterki lub wady, których długość jest znacznie większa niż pozostałe wymiary, tzn. szerokość i głębokość. Pod względem kształtu można je podzielić na dwie podstawowe kategorie – prosto- i krzywoliniowe. Odpowiadają im dwa podstawowe rodzaje pęknięć, które w zależności od przyczyn ich powstania dzielą się na: skurczowe oraz konstrukcyjne. Skurcz betonu można zdefiniować jako zjawisko zmniejszania się jego objętości spowodowane zespołem procesów chemicznych i fizycznych. W praktyce rozróżnia się trzy rodzaje skurczu: plastyczny, chemiczny i fizyczny.Pierwszy z nich związany jest z przejściem betonu z postaci plastyczno-ciekłej do stałej. Kończy się w momencie związania cementu i trwa od kilku do kilkunastu godzin. Efektem skurczu jest osiadanie betonu w szalunkach, wczesne rysy przyszalunkowe oraz nad górnymi prętami zbrojenia. Z punktu widzenia projektowania szczelin dylatacyjnych jest to skurcz nieistotny, ponieważ ich kształtowanie się następuje po jego zakończeniu.
Skurcz chemiczny spowodowany jest zjawiskiem, w którym produkty hydratacji cementu mają objętość mniejszą niż suma objętości absolutnych cementu i wody niezbędnej do jego uwodnienia. Narasta on w tempie zbliżonym do wzrostu wytrzymałości betonu na ściskanie i zależy głównie od rodzaju oraz składu chemicznego cementu. Największy następuje w ciągu 10–15 dni od wylania i zanika po osiągnięciu przez beton 80–90% wytrzymałości końcowej. Skurcz fizyczny wynika z odparowania nadmiaru wody niewykorzystanej w procesie hydratacji cementu i zachodzi zawsze wtedy, gdy istnieje niedosyt wilgotności powietrza. Proces ten w dużej mierze ma charakter odwracalny, tzn. w warunkach pełnego nasycenia wodą betonu, który uległ już skurczowi fizycznemu, obserwuje się zjawisko jego pęcznienia. Najczęściej zanika ono po ok. 3 latach.Czasowy rozkład skurczu fizycznego i chemicznego przedstawia się następująco:
- po miesiącu: 50% wartości maksymalnej,
- po 3 miesiącach: 65% wartości maksymalnej,
- po 6 miesiącach: 75% wartości maksymalnej,
- po roku: 90% wartości maksymalnej,
- po 3 latach: 100% wartości maksymalnej.
Przedstawiony poniżej wykres ilustruje wartość skurczu w zależności od grubości płyty betonowej. Wynika z niego jednoznacznie, że wraz ze wzrostem grubości płyty maleje wartość skurczu w betonie (gdzie współczynnik ks jest wielkością zależną od przekroju).
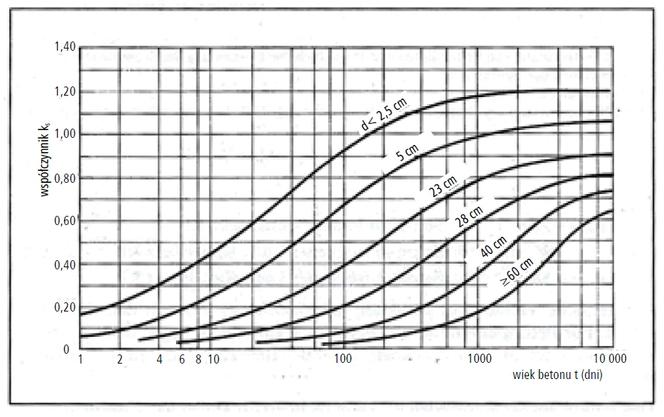
i
Poprawne zaprojektowanie szczelin dylatacyjnych w posadzkach i nawierzchniach betonowych wymaga przeanalizowania wzajemnego współdziałania i przeciwdziałania przemieszczeniom fizyczno-chemicznego skurczu betonu oraz jego odkształcalności termicznej. W tym celu konieczne jest zapoznanie się zarówno z harmonogramem budowy, jak i określenie temperatur, jakie mogą panować podczas układania betonu, jego dojrzewania oraz eksploatacji gotowej posadzki. Należy również wziąć pod uwagę długość przerwy technologicznej do momentu wykonania wypełnień dylatacji. Przy projektowaniu szczelin dylatacyjnych (zarówno pozornych, jak i konstrukcyjnych) konieczne jest również wyznaczenie minimalnej szerokości szczeliny, dobór jej kształtu, określenie maksymalnych przemieszczeń podczas rozciągania i ściskania materiału wypełniającego oraz jego dobór, uwzględniający parametry użytkowe i dopuszczalną odkształcalność roboczą. W pomieszczeniach zamkniętych powierzchnia pola elementarnego (ograniczonego szczelinami przeciwskurczowymi) nie powinna przekraczać 40 m2, a stosunek boku krótszego do dłuższego nie może być mniejszy niż 3:5. Dla pól kwadratowych wymiary nie powinny być większe niż 6 x 6 m.Osobną kategorią błędów popełnianych podczas wykonywania szczelin przeciwskurczowych jest zły dobór ich wypełnień. Do najczęściej stosowanych rodzajów kitów należą:
- poliestrowe i furanowe (mają wysoką odporność chemiczną i mechaniczną; są stosowane w przemyśle chemicznym i spożywczym),
- epoksydowo-poliuretanowe (charakteryzuje je wysoka odporność chemiczna i mechaniczna; znajdują zastosowanie w przemyśle chemicznym i spożywczym oraz w halach magazynowych, w których panuje ruch ciężki),
- poliuretanowe dwuskładnikowe (wyróżnia je wysoka odporność chemiczna i mechaniczna; używa się ich w przemyśle chemicznym i spożywczym oraz w halach magazynowych, w których panuje ruch ciężki, a także w pomieszczeniach technicznych, gdzie możliwa jest agresja chemiczna),
- poliuretanowo-smołowe (odporne na większość paliw, stosowane są w rafineriach i magazynach paliw),
- poliuretanowe jednoskładnikowe (mają bardzo dobrą wytrzymałość chemiczną i mechaniczną oraz najszersze spektrum zastosowań),
- tiokolowe (wyróżnia je dobra odporność chemiczna, przeznaczone są do zastosowań specjalnych),
- silikonowe (charakteryzują się wyższą odpornością termiczną, wykorzystywane są w pomieszczeniach sanitarnych i o stałej, wysokiej temperaturze).
Pęknięcia skurczowe mają niewielką szerokość (z reguły do 1 mm) i głębokość nie większą niż 1/3 grubości płyty. Źródłem ich pojawienia się jest najczęściej brak lub niedostateczna pielęgnacja mieszanki betonowej podczas dojrzewania, zbyt późno wykonane nacięcia posadzki, złe warunki dojrzewania betonu (np. przeciągi, duże nasłonecznienie) czy też niewłaściwy skład betonu lub nieprawidłowo dobrana ilość wody. Naprawę uszkodzeń skurczowych można wykonać dwojako, w zależności od założonego efektu końcowego:
- jeżeli chcemy uzyskać prawidłową, zamierzoną pierwotnie trasę przebiegu szczelin, istniejące rysy należy scalić poprzez wypełnienie ich sztywnym materiałem (najlepiej żywicą epoksydową), celem trwałego połączenia zarysowanych elementów posadzki. Przed wypełnieniem pęknięć żywicą należy je dokładnie oczyścić i posmarować środkiem gruntującym, a w sytuacji kiedy rysa wykazuje charakter dynamiczny, zszyć szczeliny klamrami stalowymi. Przy wyborze takiego rozwiązania konieczne jest wykonanie nowych nacięć w miejscach przewidzianych projektem i wypełnienie ich trwale elastycznym kitem, zapewniającym prawidłową pracę szczeliny;
- jeśli powstanie niezamierzonych szczelin przeciwskurczowych nie ma znaczenia dla eksploatacji posadzki, należy je lekko naciąć i wypełnić elastycznym kitem, aby zapobiec ich zanieczyszczeniu.
Przed umieszczeniem kitu w szczelinie, trzeba skorygować jej trasę poprzez nacięcie piłą kątową, dokładnie oczyścić i odkurzyć pęknięcie oraz zagruntować przeznaczonym do tego celu preparatem.Źródła powstawania pęknięć konstrukcyjnych są bardzo zróżnicowane. Wywołać je może np. brak prawidłowo wykonanego zagęszczenia podłoża gruntowego pod posadzką, jego osiadanie, źle zaprojektowana konstrukcja budynku, silne urazy mechaniczne czy zbyt mała nośność podkładu betonowego. Często spotykaną przyczyną są również warunki hydrogeologiczne występujące w miejscu lokalizacji obiektu, w którym znajduje się posadzka. Zmienny poziom wody gruntowej może powodować wypłukiwanie nośnych warstw gruntu pod podłogą, w efekcie czego dochodzić będzie do powstawania kawern i pękania nawierzchni. Jakkolwiek sposób naprawy zarysowań konstrukcyjnych uzależniony jest od prawidłowej diagnozy ich powstania, to naprawa sprowadza się najczęściej do wyrównania trasy pęknięcia widiową tarczą, wypełnienia wnętrza szczeliny szpachlówką żywiczną i „zszycia” rysy stalowymi klamrami.
Posadzki przemysłowe - uszkodzenia powierzchniowe
Do uszkodzeń powierzchniowych posadzek zaliczamy ubytki w wierzchniej warstwie posadzki, pylenie nawierzchni oraz odspojenie warstwy wykończeniowej od podłoża. Źródłem ich powstania są najczęściej przyczyny zewnętrzne związane z eksploatacją posadzki oraz wady wykonawcze i materiałowe. Przyjęcie sposobu naprawy w odniesieniu do ubytków powierzchniowych uwarunkowane jest, podobnie jak w przypadku uszkodzeń punktowych, głębokością zniszczeń. Do uzupełnienia ubytków kilkumilimetrowych stosuje się najczęściej szpachlówki żywiczne, natomiast do głębszych uszkodzeń – gotowe systemy PCC lub beton modyfikowany polimerowo. Pylenie posadzki betonowej bądź podłoża betonowego związane jest najczęściej z niską wytrzymałością betonu, błędami popełnionymi podczas realizacji lub przemarznięciem mieszanki betonowej w fazie jej wiązania. Objawia się ono szybkim wycieraniem się nawierzchni, powstawaniem kolein oraz obecnością warstwy pyłu betonowego na posadzce. Poprawę właściwości użytkowych posadzki można osiągnąć poprzez jej impregnację przy użyciu głęboko penetrującej żywicy. Z odspojeniem się posadzki od podłoża mamy do czynienia w sytuacji, kiedy obserwujemy brak przyczepności górnej, wykończeniowej warstwy do znajdującego się pod nią betonu. Uszkodzenia tego rodzaju występują we wszystkich typach nawierzchni przemysłowych, zarówno mineralnych, jak i żywicznych. Ponieważ mają one przeważnie charakter ubytku powierzchniowego, najczęściej stosowaną metodą naprawy jest aplikacja szpachlówki żywicznej.
Wytrzymałość podłoża gruntowego
Uszkodzenia spowodowane niską wytrzymałością podłoża gruntowego często są przyczyną powstawania różnicy poziomów pomiędzy pękniętymi fragmentami posadzki (np. osiadania jednego z nich lub klawiszowania na krawędziach płyt). W takiej sytuacji konieczne jest przede wszystkim ustabilizowanie podłoża i zapobieżenie dalszemu, wzajemnemu przemieszczaniu się pękniętych części posadzki. Przyjęcie sposobu naprawy zależy od rodzaju i skali uszkodzenia oraz jego źródła. Jednym z nich jest wykonywanie podlewek z materiałów cementowych o dużej płynności, mających zdolność do powiększania swojej objętości (pęcznienia) podczas procesu wiązania i dojrzewania, co gwarantuje szczelne wypełnienie przestrzeni pomiędzy podkładem betonowym a podłożem gruntowym. W sytuacjach, kiedy zniszczenia płyt betonowych są bardzo duże, a osiadanie gruntu lub kawerny przyjmuje znaczne rozmiary, może powstać konieczność skucia uszkodzonego pola i wykonania go na nowo. Taka sytuacja ma najczęściej miejsce wówczas, gdy stan techniczny posadzki uniemożliwia jej normalną eksploatację. Dopiero po wykonaniu opisanych wyżej napraw należy przystąpić do ustalenia technologii rekonstrukcji i wypełnienia szczelin dylatacyjnych.
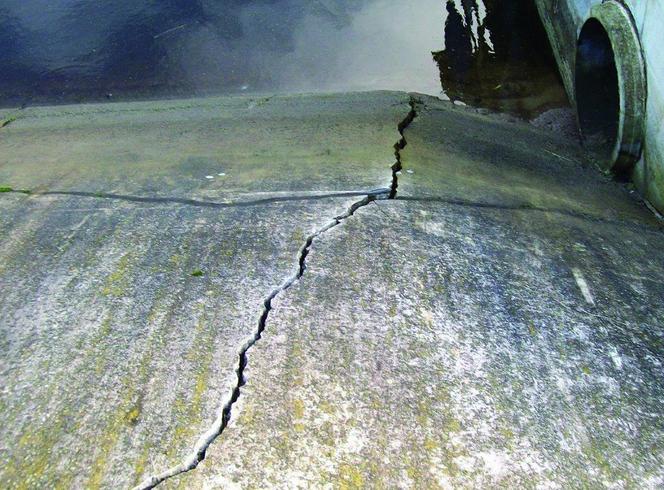
i
Wytrzymałość betonu
Wytrzymałość i parametry betonu, na którym ma być ułożona nawierzchnia, mają kluczowe znaczenie dla funkcjonowania i trwałości całej posadzki. Płyta musi być wykonana z betonu o klasie minimum C25/30, a jego wytrzymałość na odrywanie (test „pull-off”) nie może być mniejsza niż 1,5 MPa. Wartości niższe od podanych spowodują szybkie zniszczenie posadzki na skutek uszkodzenia płyty betonowej, braku przyczepności nawierzchni do podłoża itp. Beton musi być wyprodukowany w oparciu o czyste, frakcjonowane i pozbawione zanieczyszczeń oraz alkaliów kruszywo, którego maksymalne uziarnienie nie powinno przekraczać 32 mm. Wskaźnik w/c mieszanki betonowej nie może być wyższy niż 0,50, a jej receptura musi zawierać precyzyjne informacje na temat procentowej zawartości plastyfikatorów i innych ewentualnych domieszek, a także udziału i rodzaju zawartości cementu oraz wody. Kluczowe znaczenie dla odporności betonu na skurcz, a w pewnym stopniu również dla jego wytrzymałości mechanicznej, ma rodzaj oraz ilość zastosowanego zbrojenia rozproszonego. W ostatnich latach zbrojenie stalowe coraz częściej zastępowane jest zbrojeniem z tworzyw sztucznych, przeważnie z włókien kopolimerowych, które w istotny sposób modyfikują parametry fizykomechaniczne betonu, takie jak rozciąganie przy zginaniu czy ściskanie. Beton z odpowiednią zawartością takich włókien w zasadniczy sposób redukuje liczbę i średnicę szczelin przeciwskurczowych oraz znacznie wydłuża czas powstania pierwszego pęknięcia.
Patrz też: Naprawa betonu. Czym kierować się przy wyborze systemu rekonstrukcji betonu
Oprócz zaprojektowania i przygotowania odpowiedniej mieszanki betonowej na jakość podkładu wpływają również warunki cieplno-wilgotnościowe panujące podczas betonowania, w szczególności silne nasłonecznienie i przeciągi, które mogą spowodować przesuszenie nawierzchni, a w efekcie jej silny skurcz i pęknięcia. Istotne znaczenie ma również prawidłowy rozładunek i właściwe wibrowanie mieszanki betonowej. W pierwszym przypadku chodzi o możliwość rozfrakcjonowania mieszanki, jeśli będzie zrzucana z wysokości większej niż 2 m, a w drugim o pełne, systematycznie przebiegające zawibrowanie całej masy. Ostatnim z czynników warunkujących prawidłowe wykonanie podkładu jest właściwa pielęgnacja betonu, szczególnie w pierwszej fazie po jego wbudowaniu (polewanie wodą, przykrywanie folią lub natrysk środka pielęgnująco-impregnacyjnego). W przypadku źle wykonanego podkładu betonowego, np. o zbyt dużej nasiąkliwości lub zbyt niskiej wytrzymałości, ograniczoną poprawę sytuacji można uzyskać jedynie poprzez zaimpregnowanie podłoża betonowego żywicą epoksydową o niskiej lepkości, podobnie jak w przypadku pylenia posadzki betonowej. Nie gwarantuje to jednak osiągnięcia wymaganych parametrów i może być stosowane tylko do nawierzchni mniej odpowiedzialnych.
Zarysowania powierzchniowe posadzki przemysłowej
Oprócz wyżej opisanych zarysowań posadzek przemysłowych (spowodowanych skurczem betonu, uszkodzeniem konstrukcji płyty itp.) przy nawierzchniach zacieranych występuje również zjawisko zwane „pajęczą siecią” lub „wężową skórką”. Polega ono na tworzeniu się na powierzchni posadzki mikrozarysowań układających się we wzór przypominający skórę węża lub pajęczynę. Przyczyna jego powstawania wiąże się z naturą betonu oraz posadzki i nie jest wynikiem błędów wykonawczych czy też wadliwego materiału. Mikrorysy tego typu nie mają również wpływu na cechy użytkowe posadzki, a jedynie na jej wygląd. Nie są one przyczyną odspojenia nawierzchni od podłoża betonowego, natomiast ciemnieją na skutek kontaktu z wilgocią. Zjawisko to nie wymaga prac naprawczych. Jedynym zabiegiem o charakterze profilaktycznym może być wykonanie cienkowarstwowej powłoki żywicznej.
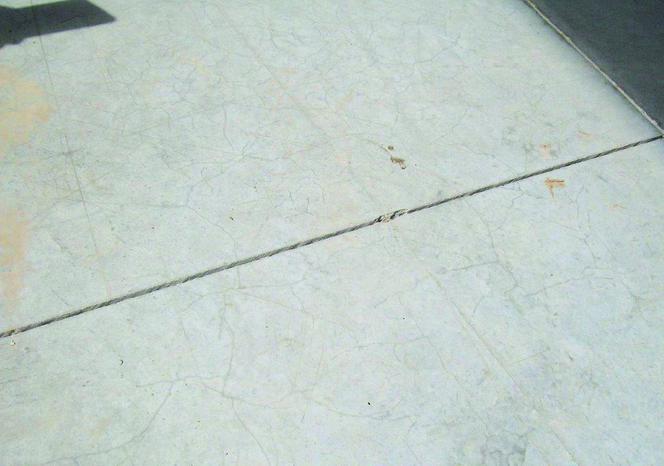
i
Podsumowanie
Opisane w artykule rodzaje i przyczyny powstawania uszkodzeń oraz sposoby ich naprawy nie wyczerpują całości zagadnienia, a jedynie podejmują próbę jego systematyki w oparciu o przyjęte na wstępie kryteria. Dostępne na rynku coraz nowsze generacje materiałów naprawczych w zasadniczy sposób skracają czas przeprowadzania napraw oraz poprawiają ich skuteczność. Celem nie powinno być jednak poszukiwanie najtańszych i najszybszych metod likwidacji uszkodzeń, lecz wykonywanie posadzek przemysłowych o jak najlepszych parametrach technicznych i jak najdłuższym okresie użytkowania, czego nie da się osiągnąć bez właściwego zidentyfikowania warunków pracy posadzki, prawidłowego wykonania jej projektu oraz fachowej realizacji.
Artykuł ukazał się w publikacji „Hale Przemysłowe”Zobacz e-wydanie
Źródło: Posadzki przemysłowe - uszkodzenia i sposoby naprawy posadzek betonowych