Spis treści
Projektowanie miejsc postojowych - unormowania prawne
Projektowanie miejsc postojowych wewnątrz budynków jest obarczone wieloma ograniczeniami, dyktowanymi w sposób ogólny, zgodnie z art. 5 ust. 1 ustawy Prawo budowlane [1],w odniesieniu do:
- nośności i stateczności konstrukcji,
- bezpieczeństwa pożarowego,
- higieny, zdrowia i środowiska,
- bezpieczeństwa użytkowania i dostępności obiektów,
- ochrony przed hałasem,
- oszczędności energii i izolacyjności cieplnej,
- zrównoważonego wykorzystania zasobów naturalnych, a także szczegółowy, m.in. poprzez zapisy § 102 do § 108, § 274 do § 281 czy § 305 warunków technicznych [2], odnoszące się do:
- gabarytów garażu,
- dojazdu i szerokości dróg manewrowych,
- wymiarów i lokalizacji stanowisk postojowych,
- dojść i ciągów komunikacji pieszej,
- dostępności dla osób niepełnosprawnych,
- instalacji wentylacji, oświetlenia,
- zapewnienia odpowiedniej akustyki przegrody,
- zagwarantowania szczelności przegrody w sposób uniemożliwiający przenikanie przez nią spalin lub oparów paliwa,
- rozwiązań wpływających na warunki pożarowe,
- posadzki.
Ta ostatnia niewątpliwie jest bardzo ważna z punktu widzenia estetyki wnętrza hali garażowej, a zarazem stanowi warstwę wyjątkowo czułą na wszelkiego rodzaju błędy związane z jej zaprojektowaniem, wykonaniem czy użytkowaniem. Nie jest to jednak element autonomiczny i, rozpatrując wszelkie zagadnienia z nim związane, trzeba brać pod uwagę cały układ podłoże-podłoga–posadzka. Tu należy zamieścić słowo wyjaśnienia i uporządkować terminologię.
Podłoże podłogi - definicja
Podłoże podłogi to, zgodnie z normą PN-EN 13318:2002 [3], „element konstrukcji nośnej budynku, na którym jest wykonywana podłoga”. Definicja ta została nieco rozwinięta w warunkach technicznych wykonania i odbioru robót budowlanych [4], gdzie przyjęła brzmienie: „poziomy na ogół element konstrukcji budynku, na którym wykonana jest podłoga (strop, płyta betonowa na gruncie) lub zagęszczony grunt (ewentualnie zdrenowany lub stabilizowany)”.
Podłoga - definicja
Podłoga, zwana też dalej „płytą posadzki” i „nawierzchnią przemysłową/garażową”, zgodnie z tymi samymi warunkami technicznymi wykonania i odbioru robót budowlanych [4], to „wielowarstwowe wykończenie podłoża, najczęściej poziomej przegrody konstrukcji budowlanej o określonych właściwościach użytkowych”. Cechy te są kształtowane przez odpowiednio dobrany układ warstw, będący w stanie przenieść obciążenia przewidywane do funkcji danego pomieszczenia (rodzaj, rozkład oraz wielkość), umożliwiający ruch (odpowiednia geometria/wytworzenie płaszczyzny), a także wpływający m.in. na: akustykę, izolacyjność termiczną i przeciwwilgociową czy dobór warstwy wieńczącej przegrodę poziomą/strop. W zależności od określonych warunków brzegowych podłogi mogą być wykonywane również jako jednowarstwowe.
Posadzka - definicja
Posadzka zaś, zgodnie z normą PN-EN 13318:2002 [3], stanowi „wierzchnią użytkową warstwę podłogi”. To po niej bezpośrednio odbywa się komunikacja. Jest również najbardziej newralgiczną powierzchnią – jej prawidłowe wykonanie, zapewniające w sposób trwały estetykę i bezpieczeństwo użytkowania, niejednokrotnie nastręcza wykonawcom kłopotów. Na efekt końcowy nakłada się bowiem szereg procesów (począwszy od fazy koncepcyjnej, przez projekt i wykonanie całego układu, na konserwacji posadzki kończąc), w które należy dodatkowo wpleść chociażby pośpiech (niedopasowanie rozwiązań do zastanej sytuacji, np. niedostateczne rozpoznanie nośności gruntu rodzimego, źle przygotowana i zagęszczona podbudowa, zbyt krótkie przerwy technologiczne, brak dopracowania detali) czy szukanie oszczędności konstrukcyjno-materiałowych (pomijanie lub niezachowanie grubości poszczególnych warstw, zmiany materiałowe powodujące brak kompatybilności układu, przelewanie wody zarobowej itd.). Przegroda spełni oczekiwania przyszłych użytkowników, jeżeli jej układ będzie prawidłowo skomponowany. Każda z warstw ma przypisaną, ściśle określoną rolę, która stanowi punkt wyjścia przy doborze jej parametrów konstrukcyjno-materiałowych.
Niezbędne jest również wzajemne dopasowanie i współpraca. Przykładową konstrukcję podłóg przedstawiono na rys. 1 i 2. W niniejszym artykule skupiono się na rozwiązaniach najczęściej wykorzystywanych w halach garażowych.
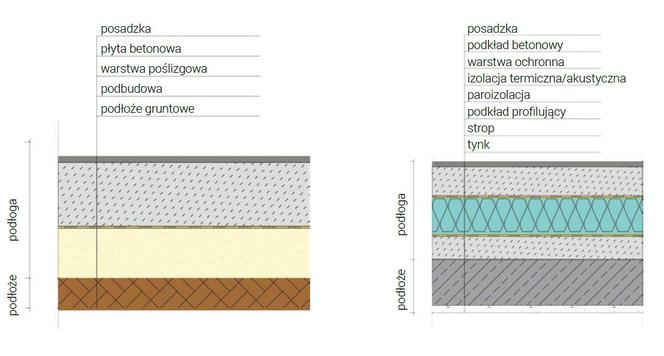
i
Podłogi w halach garażowych wielostanowiskowych
Zgodnie z warunkami wykonywania i odbioru robót budowlanych [4] wyróżnia się podłogi na podłożu gruntowym lub betonowym z warstwą rozdzielczą oraz w układzie zespolonym z podłożem betonowym.
Dla pierwszej z nich podłożem jest zagęszczony grunt budowlany, na którym najczęściej projektuje się podbudowę w postaci warstwy zagęszczonego piasku i tzw. chudego betonu lub gruntu stabilizowanego cementem. W przypadku drugiej z wymienionych płyta betonowa na gruncie lub strop żelbetowy. Podłożu gruntowemu stawia się warunki m.in. w odniesieniu do zapewnienia równomiernego osiadania pod wpływem generowanych przez przegrodę obciążeń, pożądanej nośności czy możliwości zagęszczenia do wymaganego wskaźnika. Powinno być ono równe (dopuszczalne odchyłki do 10 mm pod dwumetrową łatą) i płaskie. Podłoże betonowe (sztywne) z warstwą rozdzielczą musi być nośne, płaskie (dopuszczalne nierówności do 10 mm pod dwumetrową łatą), bez ostrych krawędzi i dziobów. Wobec podłoża sztywnego z warstwą adhezyjną – jak w przypadku dwóch wcześniejszych – stawia się warunek nośności,a także równości, dopuszczając odchyłki do 15 mm pod dwumetrową łatą. Dodatkowo, celem skutecznej aplikacji warstwy sczepnej, należy wyeliminować ewentualne lokalne osłabienia podłoża, odpowiednio oczyścić i – zgodnie ze wskazaniami producenta danego materiału/zestawu – zagruntować powierzchnię.
Tu uwaga: przy doborze produktów użytych na przegrodę powinno się uwzględnić wytrzymałość na ściskanie betonu płyty konstrukcyjnej, by w późniejszym czasie nie nastąpiło odspojenie płyty podłogi. Istotny jest również niski skurcz materiału.
Płyty posadzki garażowej, zgodnie z założeniami projektowymi, muszą przejmować i przenosić na podłoże obciążenia:
- statyczne (użytkowe, równomiernie rozłożone i punktowe),
- mechaniczne i dynamiczne (siły wywołane przejazdami samochodów, odporność na uderzenia oraz na ścieranie spowodowane kołami pojazdów samochodowych),
- termiczne (wywołane gradientem temperatury między poszczególnymi warstwami układu podłogi czy między temperaturą w momencie aplikacji materiałów przegrody a tą występującą podczas jej eksploatacji),
- wywołane skurczem betonu.
Płytom takim stawia się również wymagania m.in. w zakresie odporności pożarowej czy szczelności. Istotne jest odpowiednie określenie warunków brzegowych z punktu widzenia technicznego oraz funkcjonalności – innych dla podłogi na gruncie, a innych dla tej na stropie. W zależności od nich bowiem w układzie podłogowym pojawią się także warstwy rozdzielcze, adhezyjne, wyrównawcze, wygładzające czy materiały zapewniające odpowiednią izolacyjność:
- akustyczną – przy dźwiękach powietrznych i materiałowych izolacyjność przegrody można poprawić np. przez zwiększenie jej masy powierzchniowej czy – co jest rozwiązaniem ekonomiczniejszym – zastosowanie elastycznych materiałów o wysokiej gęstości, w układzie podłogi pływającej,
- termiczną – przy czym w przypadku materiałów użytych na tę warstwę w garażach należy zwrócić szczególną uwagę nie tylko na oczywiste własności termoizolacyjne, lecz także na pozostałe parametry, m.in. wytrzymałość na ściskanie; do jej wykonania polecany jest nienasiąkliwy polistyren ekstrudowany XPS; w odniesieniu do popularnego ze względów ekonomicznych styropianu, zgodnie z normą PN-B 20132:2005 [5], zaleca się użycie EPS 200-036 Dach/Podłoga/Parking, wytrzymującego naprężenia ściskające na poziomie min. 200 kPa przy 10-procentowym odkształceniu,
- przeciwwilgociową lub paroszczelną – dobór materiału na tę warstwę następuje m.in. w zależności od panujących warunków gruntowo-wodnych czy wilgotnościowych oraz przyjętej koncepcji architektonicznej (np. garaż w całości lub częściowo podziemny, garaż naziemny),
- pożarową.
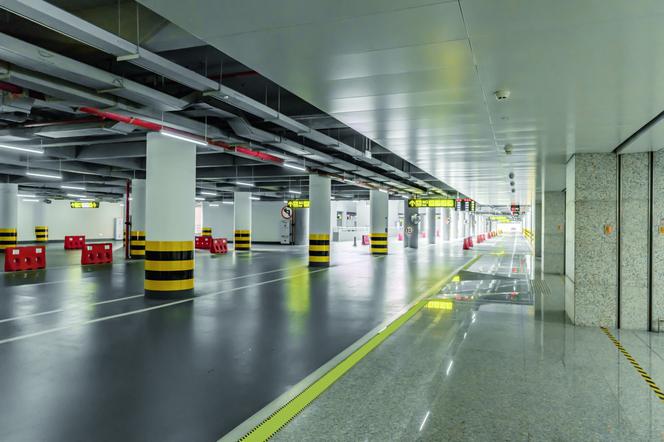
i
Ważna jest kolejność umieszczania poszczególnych warstw w budowanym układzie podłogowym, uwzględniająca parametry materiałów dobranych do ich wykonania – zwłaszcza w odniesieniu do izolacji przeciwwilgociowej, paroszczelnej, termicznej bądź akustycznej. Fakt wplecenia w układ podłogowy materiałów rozdzielczych czy izolujących w danym zakresie wymusza dodanie kolejnych wymogów konstrukcyjno-materiałowych dla pozostałych warstw układu, np. w stosunku do sztywności, grubości czy wytrzymałości na ściskanie i zginanie podkładu podłogowego umieszczonego na danej izolacji.
Podkładem podłogowym określa się natomiast, zgodnie z warunkami technicznymi [6], warstwę z materiałów podkładowych, wykonaną na budowie bezpośrednio na podłożu (jako rozlewną – wylewki, gęstoplastyczną – rozkładaną, prefabrykowaną – suchą), związaną z nim siłami przyczepności (podkład zespolony) lub niezwiązaną albo też ułożoną na warstwach pośrednich lub izolujących (podkład na warstwie rozdzielczej bądź na sprężystej warstwie izolacji – tzw. pływający) w celu:
- uzyskania określonego poziomu,
- ułożenia posadzki,
- stanowienia posadzki.
Szczeliny dylatacyjne
Bardzo ważnym zagadnieniem – w odniesieniu do całego układu podłogowego – są dylatacje, czyli szczeliny wypełnione materiałem trwale elastycznym, pozwalającym na swobodę odkształceń (przede wszystkim skurczowych, termicznych) lub wzajemnych ruchów między poszczególnymi polami. Należy zadbać o ich prawidłowe rozmieszczenie i wykonanie. Aby szczeliny dylatacyjne skutecznie przerwały łańcuch propagacji naprężeń między poszczególnymi polami, ich szerokość powinna wynosić od 4 do 12 mm [6].
Projektuje się je, uwzględniając docelowe obciążenia posadzki, wymagany stopień równości powierzchni, kształt i konstrukcję podłogi czy wielkość pól roboczych. Wyróżnić można kilka typów dylatacji:
- konstrukcyjne budynku – są niezależne od konstrukcji samej podłogi, przebiegają przez wszystkie warstwy układu;
- przeciwskurczowe (kontrolne) – wykonane na części grubości podkładu z zaprawy cementowej lub betonu, w celu wymuszenia przewidywanego rozmieszczenia rys skurczowych lub przeniesienia odkształceń spowodowanych skurczem; zgodnie z warunkami technicznymi [6] powinny być one ukształtowane w świeżej warstwie (w przypadku posadzek betonowych utwardzanych powierzchniowo – maksymalnie do 48 godzin od zakończenia zacierania) i mieć głębokość od 1/2 do 1/3 grubości posadzki w odległościach nieprzekraczających:
– 4 m w posadzkach na podłożu gruntowym w pomieszczeniach zamkniętych,
– 6 m w posadzkach usytuowanych we wnętrzach z niewielkimi wahaniami temperatury,
– 5,5 m w posadzkach usytuowanych w pozostałych miejscach;
- strefowe – robocze, na styku pól wykonywanych w różnym czasie; muszą one przechodzić przez całą grubość płyty podłogi i być odwzorowane w posadzce; wykonuje się je także w przypadku powierzchni nieregularnych, np. o kształcie litery L lub U; zgodnie z warunkami technicznymi [4] w przypadku betonowania jednej posadzki o dwóch lub więcej polach należy je połączyć za pomocą wspólnego zbrojenia prętami bądź siatką albo dyblami rozmieszczonymi w odległościach nie większych niż 40 cm, przy czym pręty powinny być z jednej strony zaizolowane w celu umożliwienia poziomego przesuwu w jednym z łączonych pól betonowych, bez możliwości ich wzajemnych przemieszczeń w pionie; warto jednak każdorazowo zastanowić się nad efektem, jaki danym rozwiązaniem chce się osiągnąć;
- brzegowe – oddzielają podłogę od elementów pionowych; przecinają warstwę wierzchnią i dodatkowo, w przypadku podłogi pływającej, zapobiegają powstawaniu tzw. mostków akustycznych;
- montażowe – oddzielają posadzkę od kratek, wpustów, rur instalacyjnych itp.
O ile dylatacje konstrukcyjne, brzegowe i montażowe są intuicyjnie przenoszone na posadzkę, o tyle w przypadku strefowych czy przeciwskurczowych nierzadko dochodzi do dyskusji z inwestorem, który chcąc uzyskać pewien efekt estetyczny, nie zawsze jest skory do ich bezpośredniego przeniesienia na powierzchnię posadzki. Dylatacje należy także wykonać w miejscu projektowanych otworów drzwiowych, zwłaszcza na styku podłóg o różnej grubości i/lub konstrukcji. Rozstaw i szerokość szczelin dylatacyjnych muszą zawsze uwzględniać właściwości materiału warstwy wierzchniej. Może się okazać, że w stosunku do konkretnych warunków brzegowych podane wyżej wymogi ulegną zmianom.
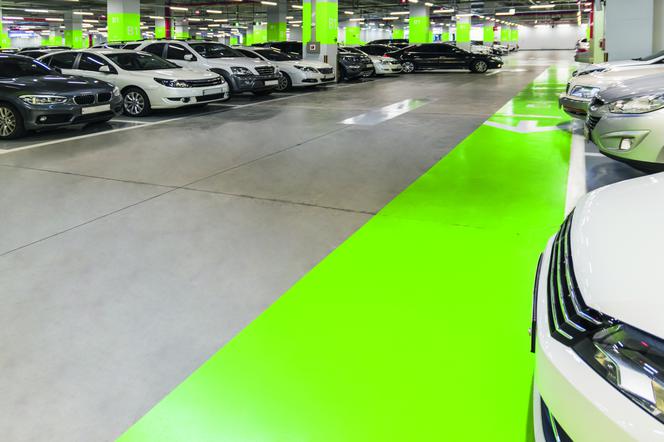
i
Wykończenie podłogi
W odniesieniu do samego wykończenia podłogi, czyli posadzki, warunki techniczne [2] narzucają konieczność wykonania odpowiednich spadków do wpustu kanalizacyjnego oraz progów o wysokości 30 mm, uniemożliwiających spływ wody na zewnątrz i na niższy poziom garażowania (z odpowiednim dostosowaniem obrzeży w miejscach komunikacji dla osób niepełnosprawnych). Dodatkowo, ponieważ jest to warstwa ostateczna podłogi, oczekuje się od niej spełnienia parametrów, które wpływają bezpośrednio na bezpieczeństwo użytkowania. Zgodnie z § 291 i § 305 ust. 1 warunków technicznych [2]:
- „Budynek i urządzenia z nim związane powinny być projektowane i wykonane w sposób niestwarzający niemożliwego do zaakceptowania ryzyka wypadków w trakcie użytkowania (…)”,
- „Nawierzchnia (…) ciągów komunikacyjnych w budynku (…), a także posadzki w garażu, powinna być wykonana z materiałów niepowodujących niebezpieczeństwa poślizgu”.
Wybierając zatem materiał, a także sposób realizacji posadzki, należy zwrócić szczególną uwagę na zapewnienie:
- równości powierzchni (odchylenie powierzchni posadzki od płaszczyzny poziomej bądź pochylonej zgodnie z warunkami technicznymi [4] powinno być nie większe niż 5 mm na całej długości lub szerokości pomieszczenia),
- odporności na pylenie,
- antypoślizgowości,
- odporności na czynniki chemiczne (m.in.: oleje mineralne, płyny hamulcowe, kwasy z baterii akumulatorowych, wodę, środki czyszczące),
- trwałości.
Dla każdej z powyższych właściwości istnieją pewne kryteria. Przykładowo zdolność posadzki do przeciwdziałania poślizgom, zgodnie z instrukcją ITB [9], wskazuje się m.in. za pomocą współczynnika przeciwpoślizgowości R oraz parametru zwanego oporem poślizgu, określającego przemieszczenie podeszwy obuwia pieszego względem nawierzchni, przy czym nie da się przełożyć bezpośrednio współczynnika R na wartość oporu poślizgu. Już na etapie projektowania należy dobrać docelowy rodzaj posadzki, spełniający oczekiwania przyszłych użytkowników, i odpowiednio dostosować pod niego cały układ.
Tab. 1. Proponowane minimalne wartości współczynnika przeciwpoślizgowości R i oporu poślizgu dla podłóg w pomieszczeniach garaży według PN-EN 13036-4:2004 [7] | |||
Przeznaczenie posadzki | Współczynnik R |
Opór poślizgu posadzki suchej mokrej |
|
Garaże, parkingi niewystawione na działanie warunków pogodowych | R10 | 65–75 | 30–40 |
Garaże, parkingi wystawione na działanie warunków pogodowych | R11 | 75–90 | 40–64 |
By osiągnąć zamierzone parametry użytkowe przegrody, kładzie się na jej wierzchnią warstwę różnego rodzaju impregnaty, suche posypki, powierzchniowe utwardzacze mineralne, wylewki cementowe czy cementowo-polimerowe. Rozwiązaniem najczęściej wybieranym na posadzkę hali garażowej jest utwardzona powierzchniowo za pomocą preparatów proszkowych i zatarta mechanicznie płyta betonowa. Wykonuje się ją jednocześnie z podkładem betonowym. Preparaty proszkowe zawierające cement i trudno ścieralne kruszywa, wcierane intensywnie w zagęszczoną mieszankę betonową, absorbują z niej mleczko cementowe, wiążąc i twardniejąc prawie jednocześnie z nią. Zgodnie z warunkami technicznymi [4] minimalna grubość utwardzonego powierzchniowo podkładu betonowego powinna być:
- minimum 3 razy większa od średnicy największego ziarna kruszywa w betonie, a jeśli występuje zbrojenie prętami – co najmniej 5 razy,
- nie mniejsza niż 30 mm dla podkładu zespolonego z podłożem,
- nie mniejsza niż 35 mm dla podkładu na warstwie rozdzielającej,
- nie mniejsza niż 40 mm dla podkładu pływającego,
- nie mniejsza niż 120 mm w przypadku posadzki betonowej przemysłowej, z ciężkim transportem.
Posadzki cementowo-polimerowe to na ogół suche mieszaniny cementów specjalnych, wypełniaczy, domieszek i dodatków,na bazie żywic epoksydowych, poliuretanowych, poliestrowych czy akrylowych. Cechują się one dużą wytrzymałością mechaniczną i zmęczeniową, odpornością na uderzenia oraz bardzo dobrą przyczepnością do podłoża. Posadzkami typu powłokowego, wylewanego i szpachlowanego, są nawierzchnie żywiczne, najczęściej na bazie żywic epoksydowych i poliuretanowych, czasem akrylowych, epoksydowo-poliuretanowych czy winylowo-estrowych. Powierzchnia podkładu podłogowego bezpośrednio przed nałożeniem posadzki żywicznej powinna być szorstka, czysta, niezatłuszczona, odznaczać się wilgotnością nie większą niż 4% oraz wytrzymałością na ściskanie nie mniejszą niż 25 MPa, przy czym każdorazowo należy przestrzegać zaleceń producenta danego materiału. Tego typu posadzki odznaczają się dużą odpornością chemiczną oraz trwałością. Łatwo nadać im również pożądane parametry użytkowe (typu antypoślizgowość)czy estetyczne (bogata kolorystyka, uzyskanie połysku/matowości powierzchni). Posadzki takie można wykonywać także jako antyelektrostatyczne. Rzadziej stosowane są posadzki w postaci okładziny ceramicznej. Można kształtować ich odpowiednie parametry użytkowe, jednak jest to rozwiązanie najbardziej praco- i czasochłonne, wymagające dużej detalizacji w celu osiągnięcia zamierzonego efektu.
Reasumując, by poprawnie zbudować układ podłogowy w hali garażowej, każdorazowo należy dobierać rozwiązania konstrukcyjno-materiałowe stosownie do konkretnych warunków brzegowych, szyjąc je na miarę potrzeb. Kluczem do sukcesu jest należyta staranność na każdym z etapów towarzyszących powstaniu podłóg garażowych – zarówno podczas projektowania, jak i późniejszej realizacji. Nie można również zapominać o odpowiedniej ich konserwacji.
Literatura
- Ustawa z dnia 7 lipca 1994 r. Prawo budowlane (DzU z 1994 r. nr 89, poz. 414, z późn. zm.).
- Rozporządzenie Ministra Infrastruktury z dnia 12 kwietnia 2002 r. w sprawie warunków technicznych, jakim powinny odpowiadać budynki i ich usytuowanie (DzU z 2019 r., poz. 1065).
- PN-EN 13318:2002 „Podkłady podłogowe oraz materiały do ich wykonania. Terminologia”.
- A. Nowacki, „Warunki techniczne wykonania i odbioru robót budowlanych. Część B. Roboty wykończeniowe. Zeszyt 8. Posadzki betonowe utwardzone powierzchniowo preparatami proszkowymi”, ITB, 2014.
- PN-B 20132:2005 „Wyroby do izolacji cieplnej w budownictwie. Wyroby ze styropianu (EPS) produkowane fabrycznie. Zastosowania”.
- A. Sokalska, Z. Ściślewski, M. Suchan, „Warunki techniczne wykonania i odbioru robót budowlanych. Część B. Roboty wykończeniowe. Zeszyt 3. Posadzki mineralne i żywiczne”, ITB, 2018.
- PN-EN 13036-4:2004 „Drogi samochodowe i lotniskowe. Metody badań. Część 4: Metoda pomiaru oporów poślizgu/poślizgnięcia na powierzchni: próba wahadła”.
- DIN 51130:1992 „Badanie powierzchni podłogi. Określenie właściwości antypoślizgowych”.
- J. Popczyk, „Śliskość. Zasady doboru posadzek”, Instrukcja ITB nr 466/2011.