Prefabrykaty mogą być wytwarzane jako elementy betonowe, żelbetowe, sprężone lub zespolone (żelbetowe bądź sprężone). Na proces produkcji składa się przede wszystkim przygotowanie form i zbrojenia, wykonanie, wprowadzenie do formy i zagęszczenie mieszanki betonowej oraz dojrzewanie betonu. Do wytwarzania betonu prefabrykowanego – podobnie jak do monolitycznego – wykorzystuje się cement, kruszywa, wodę i zbrojenie wykonane z prętów, siatek lub włókien bądź występujące w formie tzw. zbrojenia aktywnego: cięgien (strun) lub kabli. W przypadku prefabrykatów wielowarstwowych dodatkowym materiałem jest izolacja termiczna z wełny mineralnej, styropianu lub polistyrenu ekstrudowanego (XPS, styroduru). Do wykonania kompletnego prefabrykatu wykorzystywane są także dodatkowe elementy mechaniczne, konieczne do poprawnego umieszczenia zbrojenia, transportu oraz montażu prefabrykatów. To między innymi wkładki dystansowe, stabilizujące zbrojenie, elementy łączące, jak np. kotwy, kasety lub szyny z pętlami odginanymi, a także kotwy i haki transportowe oraz pokrywy do zamykania otworów. Niezbędne są również środki antyadhezyjne zapobiegające przywieraniu betonu do powierzchni form w czasie produkcji elementów.
Betony i cementy stosowane w produkcji prefabrykatów
Prefabrykaty mogą być produkowane z różnych rodzajów betonu. Ciągła kontrola mieszanki oraz możliwość utrzymania stałych warunków produkcji, pozwalają na uzyskanie betonu o wyższych parametrach (np. klasy C90/105) niż w przypadku betonu monolitycznego. W produkcji prefabrykatów istotną rolę odgrywa odpowiednio dobrany czas utrzymania właściwości roboczych mieszanki i łatwość jej zagęszczania. Znaczenie ma również możliwość uzyskania szybkiego przyrostu wytrzymałości wczesnej betonu. Wciąż udoskonalane są różne odmiany betonów specjalnych, takie jak np. samozagęszczalny (SCC), architektoniczny, fibrobeton (FRC ze zbrojeniem rozproszonym), a także z zawartością polimerów (PCC), wysokowartościowy (HPC), samoczyszczący lub transparentny. Trzy pierwsze są dość popularne, choć ich poprawne zaprojektowanie oraz wytworzenie nie jest łatwym zadaniem. Wymaga czasem wielu prób zarówno laboratoryjnych, jak i w zakładzie prefabrykacji, przed rozpoczęciem właściwej produkcji. Znanym materiałem służącym do wytwarzania prefabrykatów jest także keramzytobeton, zawierający kruszywo wytwarzane z surowców naturalnych – keramzyt.
Beton samozagęszczalny – powstaje z mieszanki betonowej o bardzo płynnej konsystencji, która zagęszcza się pod wpływem siły grawitacji. Dzięki temu prawie całkowicie ulega on odpowietrzeniu i szczelnie wypełnia formę, co eliminuje koniecz ność dodatkowego wibrowania. Samozagęszczalność mieszanki pozwala na wykonywanie prefabrykatów o gęsto ułożonym zbrojeniu oraz skomplikowanych kształtach, a także elementów architektonicznych (ze względu na możliwość uzyskania gładkiej powierzchni). Do tego rodzaju betonów stosuje się cementy portlandzkie CEM I, portlandzkie wieloskładnikowe CEM II, hutnicze CEM III oraz wieloskładnikowe CEM V. W zależności od użytego typu mieszanka będzie charakteryzowała się innym przyrostem wytrzymałości. Zawartość cementu w betonie może się wahać od 350 do 450 kg/m³.
Niezbędnymi składnikami mieszanki samozagęszczalnej są domieszki upłynniające – superplastyfikatory, dzięki którym uzyskuje ona żądaną konsystencję, oraz dodatki zwiększające łączną ilość spoiwa, zapewniającą odpowiednią lepkość mieszanki, a co za tym idzie odporność na segregację. Ponadto stosowane mogą być również domieszki stabilizujące (podnoszą odporność na segregację, ale mogą obniżyć wytrzymałość betonu). Dobór składników mieszanki betonu samozagęszczalnego, w każdym przypadku, powinien być ustalany indywidualnie w laboratorium, a później w wytwórni, w warunkach produkcji elementów.
Beton ze zbrojeniem rozproszonym (fibrobeton) – w betonie tym stosowane jest zbrojenie rozproszone w postaci włókien stalowych, polipropylenowych, polimerowych, szklanych, a także węglowych lub bazaltowych. Dzięki nim fibrobeton ma wyższą wytrzymałość na rozciąganie, nie ulega kruchemu pękaniu i nawet po osiągnięciu założonej wytrzymałości na zginanie nadal może przenosić obciążenia. Prefabrykaty są mniej podatne na zarysowanie od żelbetowych i bardziej niewrażliwe na uszkodzenia mechaniczne.
Zastosowanie włókien zapobiega skurczowi betonu i powstawaniu rys skurczowych, co poprawia szczelność i wodoszczelność wyrobu. Fibrobeton wykorzystywany jest często do wytwarzania prefabrykatów o cienkich przekrojach, np. kręgów studni, a także płyt i elementów przestrzennych do okładzin ściennych, elewacji wentylowanych i dekoracyjnych fasad o dużych powierzchniach, zarówno pełnych, jak i ażurowych.
Beton architektoniczny – pozwala uzyskać prefabrykaty o wysokiej jakości, których powierzchnia dodatkowo spełnia najwyższe wymagania estetyczne, np. jest jednolita, idealnie gładka lub jej faktura imituje inne materiały. Nowoczesne linie produkcyjne oraz powtarzalność warunków produkcji i stała ich kontrola gwarantują wykonanie elementów o bardzo wysokiej jakości. Faktury uzyskuje się np. dzięki zastosowaniu matryc drewnianych, gumowych lub z elastycznych tworzyw sztucznych, a także poprzez obróbkę mechaniczną (szlifowanie, piaskowanie, śrutowanie, łamanie). Można również odsłonić kruszywo, spłukując wierzchnią warstwę zaczynu, która w tym przypadku musi wolniej wiązać. Efekt ten uzyskuje się, nakładając opóźniacz wiązania na powierzchnię formy. Możliwa jest także produkcja betonu kolorowego. Barwę nadaje się np. poprzez zastosowanie białego cementu, wyeksponowanie kolorowego kruszywa czy naniesienie na fakturę powłoki z farby. Beton można także barwić w masie, dzięki dodaniu pigmentu do mieszanki betonowej.
Keramzytobeton – jest coraz częściej wykorzystywany ze względu na dobrą izolacyjność cieplną, akustyczną i ognioodporność. Jego głównym składnikiem jest lekkie kruszywo ceramiczne – keramzyt – otrzymywane przez wypalanie łatwo pęczniejących glin w piecach obrotowych w temperaturze 1200°C bez domieszki jakichkolwiek szkodliwych substancji. Z keramzytobetonu można wykonywać elementy o różnych kształtach i wymiarach (popularne są domy ze ścian prefabrykowanych), które, co istotne, nie wymagają specjalnego wykończenia, np. tynkowania. Cementy stosowane w prefabrykacji betonowej powinny przede wszystkim charakteryzować się szybkim przyrostem wytrzymałości wczesnej, co pozwoli na bezpieczne rozformowanie, paletyzowanie i transportowanie elementów. Zazwyczaj wykorzystywane są cementy portlandzkie, wieloskładnikowe, o wysokiej klasie wytrzymałości (zwykle 42,5 R, N lub 52,5 R), krótkim czasie wiązania oraz wysokim cieple hydratacji. Istotny jest także sposób układania mieszanki betonowej oraz warunki zapewnione na czas prac (właściwa pielęgnacja, temperatura w hali). Trzeba również uwzględnić wpływ zastosowanego cementu na urabialność mieszanki betonowej. Niektórzy producenci oferują wyroby przeznaczone do prefabrykatów, charakteryzujące się określonymi parametrami, a także wyjątkowymi cechami, np. fotokatalitycznymi (cement taki zawiera nanokrystaliczny dwutlenek tytanu TiO2), dzięki którym powierzchnia betonu ma właściwości samoczyszczące.
Dobór składników mieszanki
Składniki mieszanki betonowej do produkcji prefabrykatów dobiera się, biorąc przede wszystkim pod uwagę określone w projekcie wymagane wytrzymałości (klasę betonu, przewidywane obciążenia), wymiary i poziom skomplikowania kształtu elementu, a także jego przeznaczenie, w tym klasy ekspozycji, określające narażenie betonu na działanie agresji środowiskowych w czasie eksploatacji obiektu. Istotny jest także stopień zbrojenia oraz warunki i możliwości wytworzenia prefabrykatu. Wybór metody produkcji zależy m.in. od wielkości formowanego elementu oraz rodzaju rozwiązania konstrukcyjnego i materiałowego. Prefabrykaty o znacznej masie i wymiarach produkowane są metodą stacjonarną, natomiast mniejsze – potokowo-stacjonarną.
Mieszanka betonowa może być wprowadzana do formy np. za pomocą kosza zasypowego. Sposób jej zagęszczania (np. przy użyciu wibratorów lub stołów wibracyjnych) zależy od kształtu elementu oraz jego wielkości, a także od rodzaju zastosowanego betonu. Konieczność zagęszczania można wyeliminować, stosując mieszankę samozagęszczalną. Jeśli potrzeba, by element w szybkim czasie osiągnął wysoką wytrzymałość, mieszankę betonową można poddać obróbce cieplnej. Jest to istotne np. przy wykonywaniu elementów sprężonych, kiedy beton musi w jak najszybszym czasie uzyskać możliwość przenoszenia obciążeń od sprężenia.
Obecnie wytwórnie prefabrykatów wyposażone są w sterowane komputerowo systemy dozowania i mieszania składników oraz kontroli mieszanki betonowej podczas jej wytwarzania, co zdecydowanie ułatwia i usprawnia proces produkcji, a także zapewnia wysoką jakość wyrobów.
Rola domieszek i dodatków stosowanych w produkcji prefabrykatów betonowych
Mieszanka betonowa, z której wytwarzane są prefabrykaty powinna mieć określone właściwości. Przede wszystkim bardzo dobrą urabialność i odpowiednią konsystencję, umożliwiającą dokładne wypełnienie formy i otulenie zbrojenia przy użyciu założonej metody zagęszczania. Istotny jest również precyzyjnie określony i stały współczynnik w/c (wody do cementu) oraz odporność składników na segregację podczas zagęszczania – wówczas mieszanka zostaje skutecznie odpowietrzona. Jej właściwe zagęszczenie powinno zapewnić obniżenie jej porowatości oraz wzrost gęstości i szczelności. Bardzo ważne jest także uzyskanie wysokiej wczesnej wytrzymałości na ściskanie i rozciąganie oraz wysokiego modułu odkształcalności liniowej Younga (E).
Parametry gotowego prefabrykatu zależą w dużym stopniu od poprawnego doboru składników mieszanki oraz warunków jej wytwarzania. Dlatego bardzo istotna jest rola domieszek i dodatków stosowanych do produkcji mieszanki betonowej, dzięki którym uzyskuje ona pożądane właściwości. Mają one również wpływ na wytrzymałość prefabrykatu, trwałość oraz wygląd jego powierzchni.
Najczęściej wykorzystywane są plastyfikatory i upłynniacze, umożliwiające redukcję zawartości wody w mieszance betonowej, przy jednoczesnym zachowaniu odpowiedniej konsystencji i urabialności. Obniżone w/c pozwala uzyskać wysoką wytrzymałość betonu i korzystnie wpływa na jego trwałość. Dostępne są także domieszki powodujące krystaliczne uszczelnianie betonu, a tym samym wysoką szczelność wyrobów i ich odporność na korozję mikrobiologiczną, co jest istotne np. dla prefabrykowanych elementów wykorzystywanych do budowy sieci kanalizacyjnych. W produkcji prefabrykatów ważna jest wysoka wczesna wytrzymałość elementów, która umożliwia ich rozformowanie i przeniesienie, a w przypadku wyrobów sprężonych – zwolnienie naciągu strun. Szybsze twardnienie betonu można uzyskać, stosując nie tylko cementy o szybkim wzroście wytrzymałości, lecz także odpowiednie domieszki chemiczne (m.in. wysokiej wydajności superplastyfikatory), które przyspieszają ten proces.
Mineralne wypełniacze (np. mączka wapienna czy pył krzemionkowy) dodawane do mieszanki betonowej, w połączeniu z plastyfikatorami i innymi domieszkami, pozwalają uzyskiwać betony o coraz wyższych wytrzymałościach na ściskanie – do 45–55 MPa (dla wysokowartościowych HSC osiąga do 115 MPa, a ultrawysokowartościowych UHPC – nawet do 800 MPa).
W przypadku betonów samozagęszczalnych skład mieszanki, a zatem i zastosowane w niej domieszki, muszą jednocześnie zapewniać jej płynność, możliwość samoodpowietrzenia oraz stabilność, czyli odporność na segregację. Oprócz superplastyfikatorów wykorzystuje się także wypełniacze mineralne lub domieszki stabilizujące. W przypadku ciężkiej prefabrykacji (duże gabaryty elementów), wytwarzanej z mieszanki o niskim współczynniku w/c, stosuje się np. domieszki przedłużające czas utrzymania konsystencji, tzw. opóźniacze wiązania, które umożliwiają wydłużenie czasu układania mieszanki w formie (np. powyżej 120 min).
Wśród dodatków używanych do modyfikacji właściwości mieszanki betonowej i gotowego prefabrykatu są również polimery, żywice, a także mikrozbrojenie w postaci włókien np. szklanych, polipropylenowych, stalowych.
Rodzaje zbrojenia w elementach prefabrykowanych
Zbrojenie zazwyczaj wytwarza się w zbrojarni, a następnie przewozi do hali prefabrykacji i umieszcza w formach. Możliwe jest również rozwiązanie odwrotne – wówczas do dostarczonego zbrojenia przygotowuje się i składa formę do wykonania prefabrykatu. W zależności od rodzaju zastosowanego zbrojenia – prętów, cięgien lub włókien – prefabrykaty produkowane są z żelbetu, betonu sprężonego lub fibrobetonu. Można także wykonać elementy z użyciem różnych typów zbrojeń.
Pręty zbrojeniowe
Stal zbrojeniowa stosowana w prefabrykacji może być zwykła lub sprężająca, najlepiej o najwyższych parametrach wytrzymałościowych oraz o dużej wytrzymałości na rozciąganie, co zapewnia wysokie bezpieczeństwo konstrukcji. Do zbrojenia żelbetowych elementów prefabrykowanych zazwyczaj wykorzystuje się odpowiednio przycięte, proste lub wygięte (według projektu) pręty stalowe, które łączy się poprzez zgrzewanie, spawanie i wiązanie. Dostępne są też bardziej zaawansowane połączenia, np. zbrojenie skręcane. Stosuje się również płaskie lub przestrzenne szkielety z prętów, siatki zgrzewane bądź zbrojenie wiązane – pręty i siatki w jednym prefabrykacie.
Korzystne jest użycie półfabrykatów zbrojeniowych, które znacznie ułatwiają prace zbrojarskie. W nowoczesnych zakładach prefabrykacji proces wytwarzania zbrojenia jest zautomatyzowany i obejmuje m.in. wczytanie rysunków CAD z projektu, elektronicznie sterowane maszyny do gięcia strzemion i prętów zbrojeniowych, a także urządzenia do produkcji elektrycznie zgrzewanych siatek czy elementów przestrzennych.
Podobnie jak w konstrukcjach monolitycznych, tak i w prefabrykatach ważne jest zachowanie odpowiedniej otuliny zbrojenia. Aby miała odpowiednią grubość, stosuje się wkładki dystansowe, które odsuwają pręty zbrojeniowe od powierzchni formy. Zapewnia to również stabilność prętów i zachowanie w czasie betonowania zaprojektowanego ich rozstawu. Wkładki powinny być wykonane z materiału niereagującego z cementem i stosowanymi dodatkami, np. z polipropylenu, polietylenu lub betonu. Muszą mieć odpowiednią wytrzymałość i stabilność oraz nie przyczyniać się do korozji zbrojenia i obniżenia odporności ogniowej prefabrykatu. Ważne też, by kształt wkładek nie utrudniał otoczenia ich przez mieszankę oraz nie powodował oddzielania się betonu od wkładki. W przypadku bardziej skomplikowanego zbrojenia można wykorzystać np. ruszty lub specjalne podkładki do umieszczenia wokół otworów (w przypadku zbrojenia na przebicie).
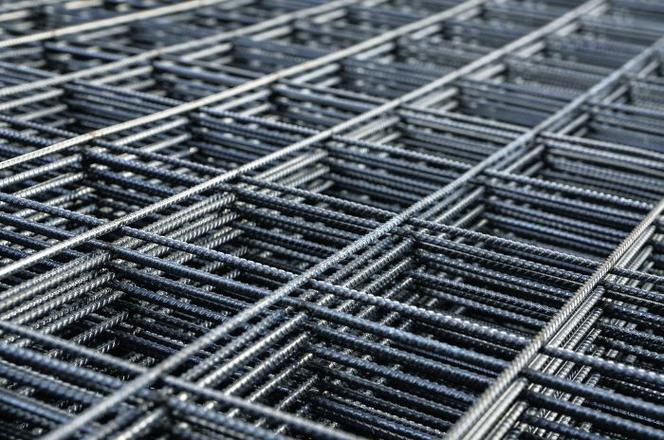
i
Cięgna i kable sprężające
W zależności od sposobu przeprowadzenia procesu sprężania elementy prefabrykowane wykonywane są ze strunobetonu lub kablobetonu. W przypadku strunobetonu stosuje się cięgna i druty ze stali sprężającej. Druty zazwyczaj skręcane są w bardzo mocne sploty (o wytrzymałości na rozciąganie nawet do 1860 MPa), które naciąga się mechanicznie lub elektrotermicznie. Cięgna i sploty pełnią w elementach sprężonych funkcje zbrojenia aktywnego. W czasie betonowania i twardnienia mieszanki mają już przyłożoną siłę sprężającą i są umocowane w konstrukcjach oporowych (metoda torów naciągowych) lub w odpowiednio przygotowanych formach (metoda sztywnych form). Właściwe sprężenie betonu następuje w chwili zwolnienia zakotwień i powoduje wówczas przekazanie sił na stwardniały beton. W ten sposób mogą być zbrojone elementy długości do 24, a w wyjątkowych przypadkach – ponad 40 m.
Przy prefabrykatach kablobetonowych naciąg cięgien następuje po zabetonowaniu. Kable sprężające (złożone z odpowiedniej liczby cięgien) są umieszczane w wykonanym w prefabrykacie kanale kablowym, naprężane za pomocą pras naciągowych oraz kotwione. Poza samym zbrojeniem w postaci kabli, do wykonania sprężenia potrzebne są wyspecjalizowane urządzenia, np. do przewlekania kabli, do iniekcji kanałów i odpowietrzania, a także zakotwienia, łączniki kabli oraz prasy naciągowe. Kable sprężające zazwyczaj stosuje się w elementach długości powyżej 12 m.
Zbrojenie rozproszone
Do jego wykonania najczęściej wykorzystywane są dość tanie włókna stalowe, o wysokiej wytrzymałości na rozciąganie i wysokim module sprężystości, które pracują w szerokim zakresie temperatur, jednak są mało odporne na korozję. Inne, często stosowane, to włókna polimerowe, które mają korzystny wpływ na pierwsze fazy dojrzewania betonu (ze względu na niski moduł sprężystości), co jednak ogranicza zakres ich wykorzystywania. Podobne parametry mają włókna szklane, ale są mniej odporne na korozję. Zaś polipropylenowe zmniejszają skurcz plastyczny i ograniczają powstawanie rys skurczowych w stwardniałym betonie, a także zwiększają jego odporność na zarysowania, które mogą się pojawić np. podczas rozformowywania elementu prefabrykowanego. Zbrojenie rozproszone w postaci włókien polipropylenowych sprawdza się zwłaszcza przy produkcji prefabrykowanych włazów do studzienek, płyt, zbiorników i innych, w których trzeba ograniczyć lub zastąpić zbrojenie metalowe. Dostępne są także – choć dość drogie i jeszcze mało popularne – włókna bazaltowe. Mają bardzo dobre właściwości mechaniczne i fizyczne, a także można je w 100% odzyskiwać wraz z betonem jako kruszywo recyklingowe.
Nie tylko stal
Dostępne jest także, choć jeszcze mało popularne ze względu na cenę, zbrojenie w postaci gładkich lub żebrowanych prętów bazaltowych, które są ok. 4 razy lżejsze od stalowych. Takie zbrojenie charakteryzuje się bardzo wysoką odpornością (do 3 razy wyższą od stali) na rozciąganie i ściskanie. Gwarantuje też bardzo dobre połączenie z betonem – zarówno mechaniczne, jak i chemiczne. Trzeba jednak pamiętać, że konstrukcje siatek i zbrojenia z prętów bazaltowych są lżejsze od betonu, dlatego powinny być odpowiednio zamocowane lub dociążone na czas zalewania i schnięcia mieszanki, co pozwoli uniknąć wyparcia ich przez beton podczas zalewania.
Nietypowym rozwiązaniem jest zbrojenie w postaci zaimpregnowanej tkaniny z wytrzymałej i sztywnej siatki z włókien szklanych (odpornych na alkalia) lub węglowych, które pozwala na tworzenie bardzo cienkich prefabrykatów, np. płyt fasadowych o grubości 50 mm. Otwory siatek muszą być większe niż maksymalna średnica ziaren kruszywa użytego do mieszanki betonowej. Tego typu zbrojenie jest bardziej wytrzymałe od stalowego i pozwala na dość duże oszczędności surowców. Do cienkich prefabrykatów betonowych zwykle stosuje się siatki stalowe lub zbrojenie rozproszone, ale materiały te można zastąpić polimerowo-bazaltowymi siatkami kompozytowymi.
Środki antyadhezyjne w produkcji prefabrykatów betonowych
Chemiczne procesy wiązania i twardnienia betonu skutkują m.in. przyczepnością stwardniałego betonu do formy. W trakcie rozformowywania elementu może zatem dochodzić do uszkodzenia powierzchni prefabrykatu lub formy, a w konsekwencji prowadzić do konieczności wykonania naprawy elementu, wytworzenia go na nowo (np. w przypadku betonu architektonicznego) bądź też do naprawy czy też wymiany formy. Generuje to dodatkowe koszty i wydłuża czas produkcji. Wyjęcie prefabrykatu z formy bez uszkodzenia wyrobu, a zwłaszcza zapewnienie powierzchni pozbawionej raków, przebarwień i plam, wymaga zastosowania odpowiednich środków antyadhezyjnych (podobnie jak w przypadku deskowań przy wykonywaniu konstrukcji monolitycznych). Zapobiegają one przywieraniu betonu do powierzchni formy, minimalizując siły spójności pomiędzy stykającymi się materiałami. Mogą być chemicznie aktywne lub bierne (czyli takie, które nie reagują ze składnikami betonu). Najczęściej wykorzystywane preparaty antyadhezyjne to substancje oleiste pochodzenia mineralnego lub roślinnego, zazwyczaj modyfikowane dodatkami poprawiającymi działanie lub aplikację środka. Mogą dodatkowo zawierać rozcieńczalniki lub występować w postaci emulsji wodnych. Stosowane są także preparaty w formie past z syntetycznymi woskami, parafinami lub żywicami. Istotną właściwością nowoczesnych środków antyadhezyjnych jest ich biodegradowalność.
Preparaty nie mogą niekorzystnie i destrukcyjnie wpływać na beton, stal zbrojeniową lub sprężającą, formę do prefabrykacji i konstrukcję. Nie powinny też oddziaływać na barwę, jakość powierzchni konstrukcji ani na poszczególne warstwy prefabrykatu. Dobiera się je zatem zależnie od materiału poszycia formy, rodzaju użytego betonu, warunków wytwarzania prefabrykatu (niektóre nie nadają się np. do obróbki cieplnej albo do stosowania w warunkach zimowych) oraz oczekiwanego wyglądu powierzchni. Nanosi się je zwykle maszynowo, za pomocą rozpylacza nisko- lub wysokociśnieniowego, ewentualnie ręcznie przy użyciu gąbek lub szczotek. Metodę dostosowuje się do postaci, konsystencji i lepkości preparatu, biorąc pod uwagę także zalecenia producenta. Środek antyadhezyjny nałożony poprawnie i w odpowiedniej ilości gwarantuje łatwe rozformowywanie matryc i uzyskanie powierzchni licowej betonu o wysokiej jakości.
Obecnie stosowane preparaty aplikuje się cienką warstwą – im cieńszą i bardziej równomierną, tym lepiej. Ich nadmiar powinien być usunięty, ponieważ może powodować zacieki i przebarwienia na gotowym prefabrykacie. Istotne jest także precyzyjne smarowanie krawędzi faktury, zwłaszcza wysokich części bocznych.
Większość środków wymaga tzw. sezonowania, które trwa od momentu naniesienia preparatu na formę do rozpoczęcia betonowania. Czas ten jest potrzebny do uzyskania właściwości antyadhezyjnych, np. całkowitego odparowania rozcieńczalnika czy wody z preparatów emulsyjnych, utwardzenia bądź polimeryzacji żywic. Dobierając odpowiedni środek antyadhezyjny oraz sposób jego aplikacji, warto wypróbować preparat w konkretnych warunkach technologicznych, przy ustalonej konstrukcji, materiale form i składzie betonu.
Normy w prefabrykacji
Produkcja prefabrykatów wymaga szczególnego przygotowania. Proces ten rozpoczyna się dużo wcześniej – już na etapie projektowania obiektu i uwzględnia np. modułowość elementów stropowych lub ściennych, a także parametry fizyczne, chemiczne i wizualne betonu potrzebnego do wykonania konkretnego prefabrykatu. Proste projekty mogą być wstępnie opracowane na podstawie wyrobów i wytycznych przedstawionych w katalogach producentów, zaś bardziej skomplikowane wymagają ścisłej współpracy architekta i konstruktora z projektantem systemu prefabrykacji. Pozwala to uniknąć problemów podczas produkcji elementów i późniejszego ich montażu.
W styczniu 2015 roku opublikowano polską wersję językową normy PN-EN 206:2014-04 „Beton – Wymagania, właściwości, produkcja i zgodność”, która zastąpiła PN-EN 206-1:2003 oraz PN-EN 206-9:2010. Obowiązuje ona producentów betonu m.in. wykorzystywanego do konstrukcji prefabrykowanych i konstrukcyjnych wyrobów prefabrykowanych stosowanych w obiektach.
W normie określono wymagania, a także ograniczenia dotyczące składników betonu, właściwości mieszanki betonowej i betonu stwardniałego oraz ich weryfikacji, specyfikacji betonu, dostawy mieszanki betonowej, procedur kontroli produkcji oraz kryteriów i oceny zgodności.
Norma PN-EN 13369:2013-09 „Wspólne wymagania dla prefabrykatów z betonu” (w wersji angielskiej) określa wymagania, podstawowe kryteria wykonawcze i zasady oceny zgodności prefabrykowanych wyrobów betonowych, żelbetowych i sprężonych, wytwarzanych z betonów zagęszczonych, lekkich zwykłych oraz ciężkich, niezawierających innych frakcji gazowych niż pobrane z powietrza. Obejmuje wszystkie wyroby prefabrykowane, które są produkowane przemysłowo – wielkoseryjnie lub indywidualnie. Może stanowić punkt odniesienia przy korzystaniu z norm szczegółowych dla konkretnych wyrobów, gdyż jest ona dla nich punktem wyjścia.
Opracowanych jest także wiele norm szczegółowych dotyczących zarówno cementów, domieszek oraz kruszyw stosowanych do produkcji betonu, a także precyzujących wymagania (np. akustyczne, termiczne, przeciwpożarowe) dla gotowych prefabrykatów (elementów ścian, stropów, schodów itp.) oraz konstrukcji z elementów prefabrykowanych.
Właściwy przebieg produkcji prefabrykatów jest kontrolowany wieloetapowo: począwszy od przygotowania, przez wykonywanie, aż po odbiór gotowych elementów. Dzięki temu wyroby z betonu prefabrykowanego w porównianiu do konstrukcji monolitycznych realizowanych bezpośrednio na budowie charakteryzuje wyższa jakość.