Spis treści
Beton - pochodzenie
Powstaje z połączenia spoiwa (cementu) rozrobionego z wodą, kruszywa (piasku i żwiru różnych frakcji) oraz ewentualnych dodatków. Prawdopodobnie po raz pierwszy został wykorzystany w Asyrii między siódmym a czwartym wiekiem p.n.e., a do jego wytworzenia jako spoiwa użyto wapna. Około drugiego wieku p.n.e. „sztuczna skała” znalazła szerokie zastosowanie w starożytnym Egipcie i imperium rzymskim, gdzie jako spoiwo stosowano popioły pochodzenia wulkanicznego, co czyniło materiał wodoodpornym.
Archeolodzy odnajdywali także ślady „betonu” w ruinach świątyń Majów. Swoją współczesną postać zawdzięcza wynalezieniu cementu portlandzkiego opatentowanego w 1824 roku przez Anglika Josepha Aspdina. Wynalazek spowodował odejście od tradycyjnych technologii budowlanych, w tym rezygnację z użycia innych wcześniej stosowanych spoiw. Kolejnym krokiem milowym dla budownictwa było wynalezienie w 1849 roku żelbetu, który łączy zalety betonu i stali, i do dziś jest najszerzej wykorzystywanym materiałem konstrukcyjnym. Sam beton poza konstrukcjami znajduje także liczne zastosowania w wyrobach takich, jak bloczki, pustaki, materiały elewacyjne, wykończeniowe i nawierzchnie.
Beton w liczbach
Roczna światowa produkcja betonu wynosi 10 mld ton, natomiast cementu portlandzkiego ponad 4 mld ton. Od lat 50. produkcja roczna cementu wzrosła dziewięciokrotnie. Ekspansja przemysłu cementowego szczególnego tempa nabrała po roku 2000 i mimo obecnego chwilowego spowolnienia przewiduje się dalszy wzrost związany z rozwojem krajów azjatyckich i afrykańskich. Aktualnie największymi producentami cementu są Chiny i Indie wytwarzające odpowiednio ok. 55% i 8% światowych zasobów (Europa – 6,6%). Równolegle, w tym samym tempie, następuje wzrost wytwarzanej ilości stali, której w 1950 roku produkowano 200 mln ton, w 2005 roku przekroczono 1 mld ton, a w 2021 roku 1,8 mld tony.
Ślad węglowy betonu
Mimo wiele ważnych dla budownictwa cech, beton i żelbet są jednocześnie materiałami, których produkcja powoduje ogromne obciążenie dla środowiska. Produkcja jednego metra sześciennego betonu na bazie cementu portlandzkiego (OPC – Ordinary Portland Cement) wiąże się z emisją 300 kg gazów cieplarnianych (w przeliczeniu na ekwiwalent dwutlenku węgla, CO2eq). Takiej objętości betonu we współczesnych konstrukcjach przeważnie towarzyszy też ok. 100 kg stali zbrojeniowej, w trakcie produkcji której do atmosfery wydostaje się kolejnych 200 kg CO2eq.
Według danych Komisji Europejskiej produkcja betonu odpowiada za 5%, a zgodnie z innymi zestawieniami nawet 8,5% światowej rocznej emisji gazów cieplarnianych. Kolejne 8% pochodzi z produkcji stali, której 52% znajduje zastosowanie w budownictwie i infrastrukturze. Aby zrealizować założony w Porozumieniu Paryskim cel ograniczenia emisji CO2 o 30% do 2030 roku i osiągnąć zerowe emisje netto w roku 2050, zarówno przemysł cementowy, jak i hutniczy będą musiały przejść gruntowną transformację.
Czym zastąpić cement?
W przemyśle stalowym od lat trwają prace nad zwiększeniem efektywności procesów produkcyjnych oraz wprowadzeniem nowych technologii mających spowodować ograniczenia emisji. Dzięki recyklingowi stali jej ślad węglowy można obniżyć mniej więcej o połowę. Kolejne redukcje osiąga się poprzez zamianę tradycyjnych pieców hutniczych na elektryczne łukowe, które mogą być zasilane z odnawialnych źródeł energii lub „czystego” atomu. W ten sposób już obecnie wytwarzana jest „niskoemisyjna” stal, jednak jej udział w całkowitej produkcji to zaledwie ok. 1%. W przypadku betonu obniżanie emisji także przebiega wielotorowo. Ścieżka dojścia do zerowej emisyjności obejmuje ograniczenie użycia cementu portlandzkiego, zastosowanie zielonej energii elektrycznej, zmniejszenie emisyjności transportu, ale najważniejszymi czynnikami w tym procesie są wykorzystanie niskoemisyjnych paliw i wychwytywanie CO2 uwalniającego się w trakcie wytwarzania.
Polecany artykuł:
Cement portlandzki powstaje z klinkieru, którego produkcja wymaga dużych nakładów energii. Konieczna jest ona do wypiekania, zmielenia i wymieszania składników. Większość emisji pochodzi jednak z samego procesu wypiekania wapienia (węglanu wapnia), co skutkuje powstaniem dwutlenku węgla. Wynika to wprost z reakcji chemicznej zachodzącej w piecach rozgrzanych do temperatury 1000ºC (CaCO3 -> CaO + CO2). Dlatego główne wysiłki koncentrują się na ograniczaniu zapotrzebowania na cement portlandzki poprzez zastępowanie go w mieszankach betonowych innymi materiałami, które mogą spełniać rolę spoiwa, a charakteryzują się niższym śladem węglowym. Do tego celu służą chociażby takie naturalne materiały, jak piasek i pył wulkaniczny lub produkty uboczne z procesów przemysłowych, np. żużel wielkopiecowy – odpad z produkcji stali, czy popioły lotne. Dzięki ograniczeniu ilości cementu portlandzkiego w składzie mieszanki betonowej o 40%, a czasem nawet 80-90% można uzyskać beton, który charakteryzować się będzie nawet o połowę (lub więcej) niższym śladem węglowym w stosunku do materiału opartego w stu procentach na zwykłym cemencie portlandzkim (OPC). Niestety zastosowanie takiego rozwiązania na dużą skalę wydaje się mało realne z powodu ograniczonej dostępności zamienników.
Odmiany cementu o wysokiej zawartości żużla wielkopiecowego czy popiołów lotnych są zresztą znane w budownictwie i chętnie wykorzystywane od wielu lat za sprawą ich innych pożądanych cech, takich jak odporność na korozję chemiczną, niski skurcz, czy niska temperatura wiązania. Obecnie zyskują szerszy rozgłos z uwagi na mniejszy wpływ na środowisko, a co za tym idzie częściej będziemy borykać się ich deficytem na rynku. Wygaszanie tradycyjnych pieców hutniczych i zastępowanie ich elektrycznymi piecami łukowymi oraz odchodzenie od kopalnych źródeł energii, przy jednoczesnym wzroście zapotrzebowania na beton, ten deficyt będzie potęgowało.
Poszukiwania nowych zamienników dla cementu portlandzkiego trwają. Producenci i wiele placówek naukowych traktuje priorytetowo badania nad składem betonu, który mógłby znaleźć szerokie zastosowanie w budownictwie. Oznacza to zwiększenie liczby używanych już zamienników, poszukiwanie innych, tradycyjnych materiałów, takich jak cementy bazujące na tlenku magnezu, jak i badania niewykorzystywanych wcześniej substancji. To np. kalcynowana glina, pochodzący z recyklingu granulat szklany lub dodatki organiczne, m.in. biowęgiel.
To produkt pirolizy, czyli wygrzewania w wysokiej temperaturze biomasy w środowisku beztlenowym. Domieszka biowęgla powoduje obniżenie wytrzymałości betonu, więc jego zastosowanie rozważane jest np. w elementach wypełniających. Eksperymenty w zakresie konstrukcji polegają na wytwarzaniu elementów ze strefami o zróżnicowanej wytrzymałości, których układ odpowiada rozkładowi sił.
W poszukiwania zastosowań dla tej technologii angażują się także architekci. W ramach współpracy firmy Snøhetta z Norwegian University of Science and Technology, dostawcami betonów i odpadów drewnopochodnych narodził się pomysł produkcji ścian złożonych z warstw o różnej nośności.
Podobne próby prowadzone są jako część badań Institute for Advanced Architecture of Catalonia w obrębie programu Carbon Copies. Poza fazę R&D ma wyjść współfinansowana przez UE, w ramach mprojektu ECO-Binder, technologia bazująca na mieszance BYF (Belite-Ye’elimite-Ferrite). Pozwala ona obniżyć ślad węglowy betonu o 25-30%. Na rynku europejskim rozważane jest użycie tej technologii w elementach prefabrykowanych. Stosowanie jej w przypadku betonu wykonywanego na budowie wymaga dalszych badań, mających na celu zwiększenie kontroli procesu wiązania. Poszukiwanie efektywnych zamienników OPC, poza dotychczas stosowanymi popiołami lotnymi i żużlem, jest jeszcze w dużej mierze przed nami. W pewnym stopniu do redukcji emisji związanych z produkcją cementu może przyczynić się obniżenie emisyjności transportu i używanej w procesie produkcji energii elektrycznej. Istotnym czynnikiem byłoby więc tu m.in. poszukiwanie alternatywnych, niskoemisyjnych paliw.
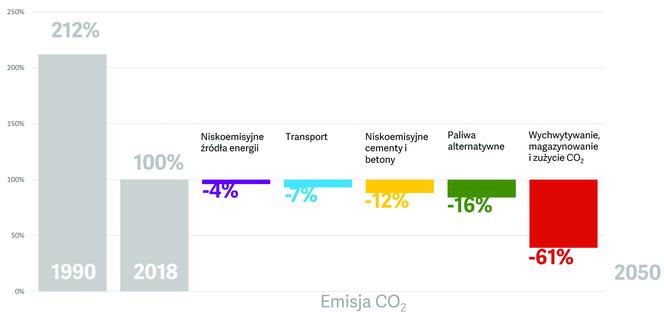
i
Beton - nowe technologie w fazie badań
Ścieżki dekarbonizacji dla krajów europejskich zakładają zwiększenie procentu energii uzyskiwanej z biomasy, zastosowanie wodoru i poszukiwanie technologii wypalania bazujących na niskoemisyjnej elektryczności. Scenariusze zakładają też zastosowanie metod wychwytywania i magazynowania CO2 (Carbon Capture Utilisation and Storage – CCUS), które są jeszcze w fazie badań. Rozwój tych technologii jest kluczowy, bo mają one odpowiadać za redukcję śladu węglowego o 40%, a według ścieżki brytyjskiej nawet o 60%.
Konieczne jest opracowanie sposobów wychwytywania CO2 w ramach procesu produkcji, budowa rurociągów, znalezienie miejsc do jego składowania lub możliwości wykorzystania. Dotychczas proces wyłapywania stosowany był tylko w projektach pilotażowych, a budowę pierwszej pełnowymiarowej instalacji rozpoczęto dopiero w 2020 roku w cementowni Brevik w Norwegii. Jej uruchomienie planowane jest na rok 2024. Doświadczenia tam zdobyte posłużą do wdrożenia technologii w kolejnych zakładach. Następnym pytaniem jest, co zrobić z wyłapanym CO2 i czy jego magazynowanie jest właściwym rozwiązaniem problemu.
W stronę efektywności betonu
Obecnie najlepszą receptą na ograniczanie wpływu betonu na środowisko jest wykorzystywanie go w bardziej efektywny sposób. W typowym kilkukondygnacyjnym budynku komercyjnym lub mieszkalnym konstrukcja odpowiada za nawet do 50% „wbudowanego” śladu węglowego określonego dla całego cyklu życia budynku (fazy od A do C), natomiast na resztę składają się fasada, instalacje i wyposażenie oraz nienośne przegrody wraz z wykończeniem. Chcąc ograniczyć ślad węglowy, warto skupić się w pierwszej kolejności na rozwiązaniu konstrukcji stropu. Najprostszym zabiegiem pozwalającym na zmniejszenie potrzebnego tu materiału jest ograniczenie rozpiętości.
O ile budynki mieszkalne charakteryzują się przeważnie umiarkowanymi rozpiętościami stropów, podyktowanymi przez optymalne wielkości pomieszczeń oraz ich regularny układ, o tyle w przypadku obiektów biurowych czy handlowych od wielu lat obserwujemy wzrost rozpiętości uzasadniany zwiększeniem elastyczności wynajmowanych przestrzeni. Jak wykazały analizy opracowane w ramach badań nad śladem węglowym konstrukcji, zwiększenie siatki słupów z rozstawu 6,5 x 6,5 m na 7,5 x 7,5 mmoże prowadzić do podwojenia śladu węglowego konstrukcji stropu w przeliczeniu na jego powierzchnię.Dalsze zwiększenie rozstawu podpór, do np. 9 x 9 m, przełoży się nawet na 4-krotny wzrost śladu węglowego stropu w stosunku do wyjściowego układu podpór.
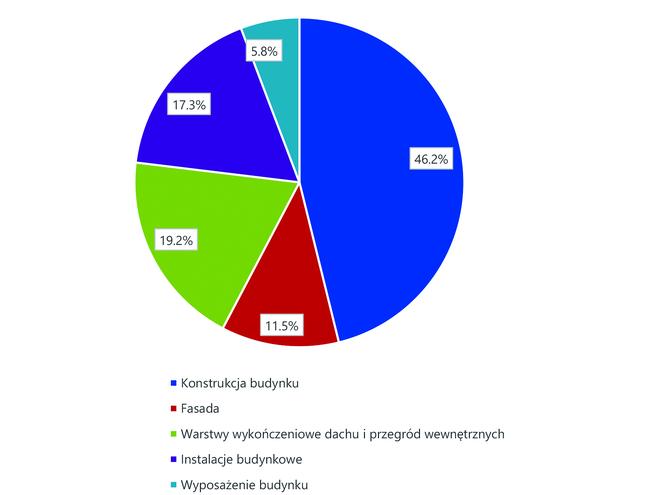
i
Chcąc zredukować ślad węglowy konstrukcji, warto też zrewidować założenia projektu dotyczące dopuszczalnych ugięć stropu czy zarysowań – dopuszczenie większego ugięcia lub większej rozwartości rys pozwoli ograniczyć ilość potrzebnej stali zbrojeniowej.
Kolejnym czynnikiem jest tzw. wysokość konstrukcyjna. Im większa wysokość konstrukcyjna elementu, tym większa jego sztywność, a w konsekwencji ilość potrzebnego materiału spada. W przypadku płyty płaskiej wysokość konstrukcyjna to po prostu jej grubość, dlatego samo zwiększenie wysokości konstrukcyjnej nie prowadzi do redukcji potrzebnego materiału. Zwiększenie wysokości konstrukcyjnej daje najlepsze rezultaty w stropach belkowych, w których główną funkcję nośną pełnią podciągi – pozwala to zwiększyć nośność stropu bez znacznego wzrostu objętości betonu. Niestety, tego typu rozwiązania nie są obecnie preferowane w budownictwie z uwagi na zmniejszenie wysokości kondygnacji w świetle konstrukcji, utrudnione rozprowadzenie instalacji wewnątrz budynku, a także bardziej złożony proces budowy w porównaniu z zastosowaniem płaskiej płyty.
Nawet w przypadku takiego stropu można ograniczyć ślad węglowy, zwiększając grubość, a to za sprawą użycia tzw. wkładów odciążających, które wypełniają przestrzeń w środku przekroju płyty, gdzie beton pracuje najmniej efektywnie, generując głównie zbędny ciężar. Wkłady te mogą mieć postać tradycyjnych pustaków, wyciętych ze styropianu bloków lub plastikowych form, które po złożeniu tworzą w płycie pustkę powietrzną. Ponieważ technologia ta pozwala pogodzić zalety płaskich płyt z korzyściami generowanymi przez zwiększenie wysokości konstrukcyjnej, jak w przypadku stropów belkowych, powstaje obecnie dużo produktów, które mogą być wykorzystane w nowo projektowanych budynkach. Tego typu stropy znalazły zastosowanie m.in. w realizacji Stadionu Narodowego oraz Muzeum Sztuki Nowoczesnej w Warszawie.
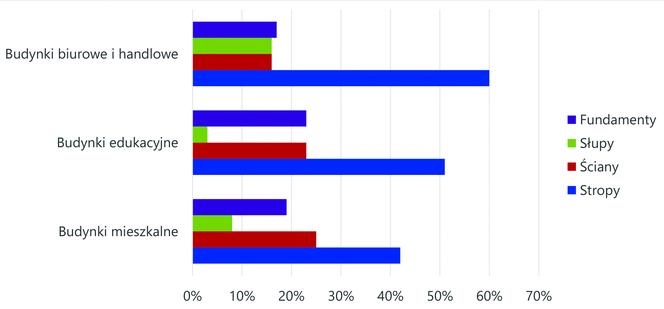
i
Poza udoskonalaniem znanych od lat systemów, trwają także badania nad nowymi, które w jak największym większym stopniu pozwoliłyby wykorzystać materiały pozyskane z recyklingu. Jednym z przykładów takich pionierskich rozwiązań, służących minimalizacji zużycia betonu, są doświadczenia prowadzone przez uniwersytet ETH w Zurychu. Autorzy badań eksperymentują z wysokiej wytrzymałości betonem zbrojonym włóknami, który wypełnia przestrzenie między wkładami z mineralnej pianki stworzonej na bazie odpadów z recyklingu i układanej w deskowaniu przez robotyczne ramię.
Inną metodą zmniejszania ilości betonu w budynkach jest zastępowanie go różnymi materiałami, które pełnią daną funkcję równie lub bardziej efektywnie. Dla omawianych wyżej stropów alternatywą mogą być prefabrykowane płyty żelbetowe zespolone z drewnianymi belkami. Tego typu rozwiązanie pozwala nie rezygnować z zalet betonu, do których należy wysoka izolacyjność akustyczna, a jednocześnie ograniczyć jego zużycie na rzecz drewnianych belek. Pod warunkiem zachowania umiarkowanych rozpiętości stropu, spełniają one swoje zadanie równie dobrze, co elementy stalowe lub betonowe, natomiast cechują się znikomym śladem węglowym. Przykłady budynków, w których zastosowano technologię hybrydową, to berliński Edge czy Hamburski Timber Pioneer.
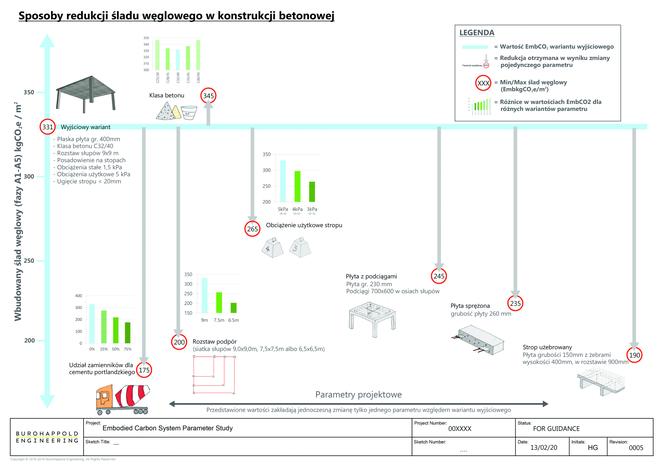
i
Kolejnym elementem wymagającym użycia dużej ilości betonu (oraz stali zbrojeniowej) są części podziemne. Wszystkie przegrody zewnętrzne takich kondygnacji będą wymagały grubości od 50 cm do czasem nawet 1 m, aby oprzeć się parciu gruntu lub sile wyporu wody gruntowej. Za sprawą tych dwóch czynników w budynkach z 2-3 kondygnacjami podziemnymi i 7-8 nadziemnymi połowa całej objętości betonu będzie musiała znaleźć zastosowanie właśnie w konstrukcji części podziemnej. Rezygnacja z niej pozwoliłaby zatem na znaczne ograniczenie wbudowanego śladu węglowego.
Ostatnią kategorią elementów, na które warto zwrócić uwagę, próbując ograniczyć ślad węglowy są ściany. Ich udział w całości konstrukcji budynku jest relatywnie wysoki zwłaszcza w obiektach mieszkalnych, głównie za sprawą przegród między pomieszczeniami mieszkalnymi i stawianym im wymaganiom akustycznym oraz przeciwpożarowym.
Po dokładnej analizie projektu może okazać się, że w miejscu pełnej żelbetowej ściany daje się wykonać słupy odpowiadające za funkcję nośną przegrody, natomiast jako jej wypełnienie zastosować materiały, które nie muszą cechować się tak wysoką wytrzymałością, jak beton.
W tym kontekście najbardziej obiecująco przedstawiają się bloczki z betonu konopnego. Beton konopny to mieszanka wapna, wody i tzw. sieczki konopnej. W odróżnieniu od tradycyjnego betonu do jego wytworzenia przeważnie nie wykorzystuje się cementu, natomiast kruszywo zastępują wysuszone i posiekane łodygi konopi przemysłowej. Brak cementu w oczywisty sposób wpływa na zdecydowane obniżenie śladu węglowego, natomiast dodatek konopi, która w trakcie swojego wzrostu pochłania dwutlenek węgla z atmosfery w procesie fotosyntezy, powoduje, że ślad węglowy takiego materiału jest bliski zeru. Niestety, z uwagi na brak cementu i kruszywa bloczki te charakteryzuje niewielka nośność. Jako materiał konstrukcyjny nie mogą one więc konkurować ze zwykłym betonem, poza niektórymi wyjątkami z obszaru budynków mieszkalnych jednorodzinnych.
W przypadku ścian wypełniających i osłonowych jest to jednak interesująca alternatywa dla konwencjonalnych materiałów, także za sprawą dobrej izolacyjności termicznej, odpowiednich właściwości akustycznych, dyfuzyjności oraz niepalności.
Beton a założenia gospodarki cyrkularnej
Trwają prace nad możliwościami dostosowania konstrukcji betonowych do założeń gospodarki cyrkularnej. Zachowane w dobrym stanie obiekty żelbetowe można poddać renowacji i wykorzystać ponownie. Adaptacja istniejącej architektury jest najbardziej efektywną metodą pod względem ograniczania emisji gazów cieplarnianych. Przyjmowany do obliczeń cyklu życia budynku czas jego funkcjonowania to przeważnie 50-60 lat, jednak niestety łatwo znaleźć przykłady obiektów w dobrym stanie technicznym, które wyburza się już po 20 latach. Potencjał konstrukcji monolitycznej w momencie rozbiórki jest ograniczony (w odróżnieniu od stali, która może zostać poddana recyklingowi w blisko 100%). Niestety, gruz betonowy po wcześniejszym pokruszeniu najczęściej jest wykorzystywany jako materiał do zasypania wykopu albo, w najlepszym razie, jako kruszywo do podbudowy dróg. Mimo że z historii znane są przypadki użycia na dużą skalę kruszyw z recyklingu, np. w trakcie powojennej odbudowy Warszawy, obecnie, aby mogły one znaleźć zastosowanie w betonie konstrukcyjnym, muszą przejść rygorystyczne badania.
Laboratoriów, które je przeprowadzają jest niewiele. Duże odległości pokonywane przez gruz betonowy w celu pokruszenia na odpowiednie frakcje, a następnie na badania, sprawiają, że takie rozwiązanie nie jest ekonomicznie uzasadnione. Korzyści dla środowiska także stoją pod znakiem zapytania. Zupełnie inaczej wyglądałaby przyszłość betonowych konstrukcji, gdyby rozwiązania projektowe uwzględniały przyszły demontaż (Design for Disassembly – DfD). Były oparte na prefabrykacji i systemie stworzonym z myślą o rozbiórce budynku bez uszkodzenia elementów.
Dodatkowo modułowość dałaby możliwość ich ponownego wykorzystania bez konieczności przetworzenia. Tego typu rozwiązania można łatwo wyobrazić sobie w przypadku powtarzalnych obiektów halowych i magazynowych, trudniej w budynkach biurowych i mieszkaniowych.
Polecany artykuł:
Beton - wyzwania na przyszłość
Problematyka ograniczenia śladu węglowego betonu i żelbetu łączy wiele zagadnień i branż. Wyzwania, które stoją przed tą gałęzią przemysłu, będą wymagały zmian zarówno w zakresie składu materiału, modyfikacji metod produkcji, poszukiwania alternatywnych źródeł energii czy w końcu sposobów wychwytywania i magazynowania CO2. Należy tu podkreślić także rolę architektów, projektantów konstrukcji i inwestorów, którzy odpowiadają za funkcję, kształt, wybór technologii lub materiałów.Poprzez swoje decyzje mogą wpływać na ilość zastosowanego betonu w projekcie, wybrać adaptację zamiast wyburzenia oraz poszukiwać rozwiązań pozwalających na późniejsze ponowne użycie elementów budynku.
Magda Pios, Wiktor Kowalski